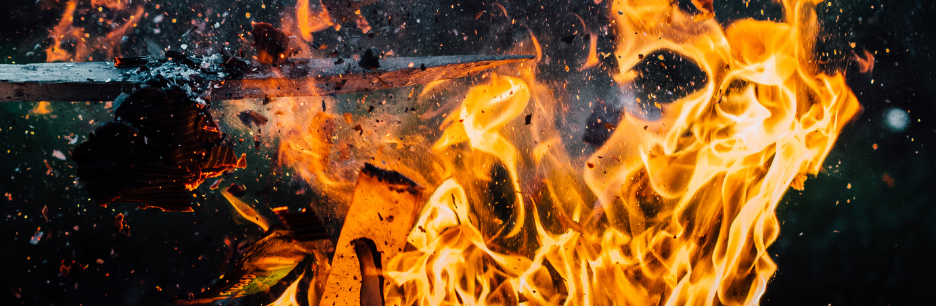
WHEN IS AN EXPLOSION-PROOF CHILLER NECESSARY?
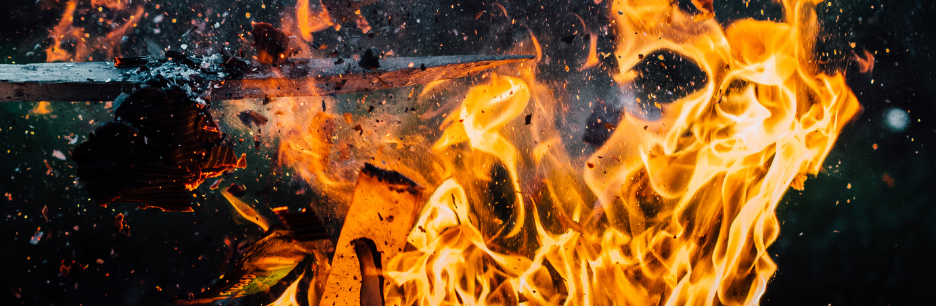
In industrial and hazardous environments, safety is paramount. Many industries handle flammable or explosive substances, making the risk of potential accidents a significant concern. When it comes to cooling equipment, such as chillers, the need for safety becomes even more critical. Enter the explosion-proof chiller – a specialized cooling solution designed to ensure maximum safety in hazardous locations.
The Importance of Explosion-Proof Cooling Equipment
In industries where safety is paramount, an explosion-proof chilling unit is more than just a cooling system; it’s a vital safeguard against potential disasters. From hazardous environments with flammable substances to laboratories handling volatile materials, these specialized chillers play a pivotal role in protecting lives, assets, and operations.
By ensuring compliance with industry regulations and offering robust safety features, explosion-proof coolers are a must-have for any organization committed to maintaining the highest safety standards in their cooling processes.
Different Types of Explosion-Proof Cooling Units
Industrial chillers are designed to operate safely in hazardous environments where flammable gases, vapors, or dust particles may be present. Here are brief descriptions of different types of chillers for explosive industrial applications:
- Air-Cooled Chillers: Air-cooled chillers are designed to dissipate heat through air-cooling mechanisms. They use fans to blow ambient air over the refrigerant coils to achieve cooling.
- Water-Cooled Chillers: Water-cooled chillers use water as a cooling medium to remove heat from the refrigerant. They require a continuous water supply, usually from a cooling tower or another water source, to carry away the heat generated during the cooling process.
- Absorption Chillers: Instead of using mechanical components, absorption chillers rely on a chemical process to cool the refrigerant. These chillers are often used in locations where electricity is limited or unavailable, as they can be fueled by natural gas, propane, or other renewable energy sources.
- Scroll Chillers: This type of chiller utilizes scroll compressors, which are known for their simplicity and reliability. Scroll compressors operate by trapping chiller refrigerant between two spiral-shaped scrolls, compressing it, and then delivering it to the condenser for cooling.
- Centrifugal Chillers: Centrifugal chillers use centrifugal compressors to circulate refrigerant and manage temperature. These chillers are popular for large-scale industrial applications due to their high-efficiency capabilities and ability to handle heavy cooling loads.
Each type of explosion-proof chiller has its own advantages and considerations depending on the specific needs of the hazardous environment where it will be installed. It is important to consult with experts and consider regulatory requirements to select the appropriate type of chiller for a particular application.
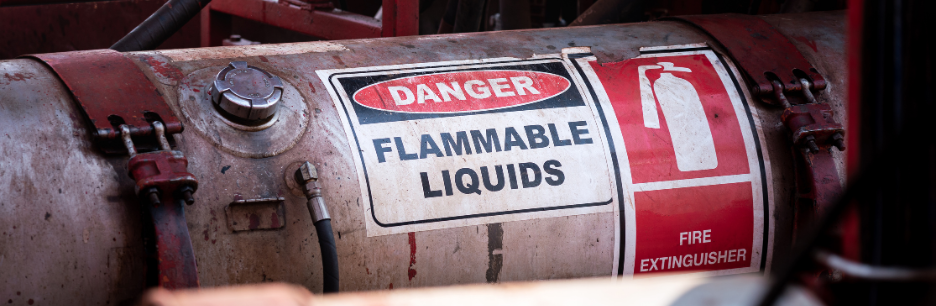
Understanding Explosion-Proof Classes
Explosion-proof classification refers to a safety standard and system designed by the National Electric Code (NEC) to mitigate the risk of explosions in hazardous environments. Such environments may contain flammable gases, vapors, dust, or combustible materials. This classification involves categorizing electrical equipment and devices based on their ability to withstand and contain any potential explosion within their enclosure.
By adhering to the hazardous area classifications, industries such as oil and gas, chemical processing, mining, and manufacturing ensure the protection of personnel and assets, reducing the likelihood of catastrophic incidents and maintaining operational integrity in high-risk settings.
Explosion Proof Classifications |
|
Class |
Definition |
Class I |
For hazardous locations containing flammable gases or vapors. |
Class II |
For hazardous locations with combustible dust. |
Class III |
For hazardous locations where ignitable fibers or flyings are present. |
Division |
|
Division I |
Designates locations where explosive materials are present under normal operating conditions. |
Division II |
Designates locations where explosive materials are handled or stored but are confined and controlled. |
Group (Class I) |
|
Group A |
Atmospheres containing acetylene. |
Group B |
Locations containing hydrogen, or gases of equivalent hazard, such as manufactured gas. |
Group C |
Locations containing ethyl-ether vapors, ethylene, or cyclopropane. |
Group D |
Locations containing gasoline, naphtha, hexane, benzine, butane, benzol, acetone, alcohol, lacquer solvent vapors, or natural gas. |
Group (Class II) |
|
Group E |
Locations containing metal dust, including aluminum, magnesium, and their commercial alloys and other similarly hazardous metals. |
Group F |
Locations containing coal, carbon black, or coke dust. |
Group G |
Locations containing starch, flour, or grain dust. |
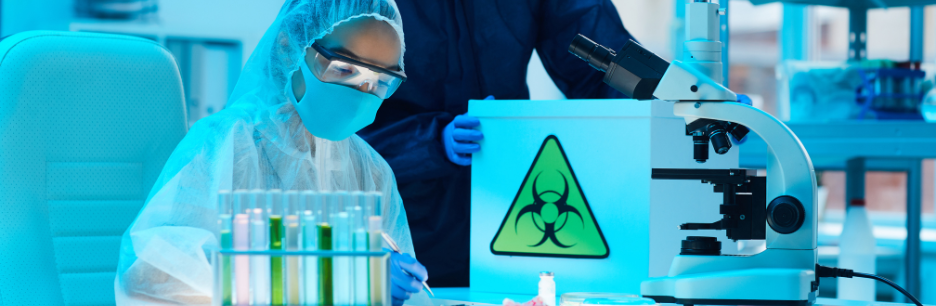
What Applications Require An Explosion-Proof Chiller?
The importance of explosion-proof chillers cannot be overstated in environments with hazardous materials or volatile substances. These specialized chillers are designed to withstand the unique challenges posed by such conditions while ensuring optimal cooling performance. Applications that typically require these cooling systems include:
Flammable or Explosive Atmospheres
In environments with flammable gases, vapors, or dust, even a tiny spark or heat source can lead to catastrophic consequences. Industries like oil and gas, petrochemical, pharmaceutical, and chemical handling frequently encounter hazardous atmospheres. An industrial chiller is essential in these environments to prevent potential ignition sources, ensuring safety for personnel and equipment.
Cooling Equipment Near Combustible Materials
Certain industrial processes involve handling volatile or combustible materials, which might release heat during processing. Placing conventional chiller units in close proximity to such materials can be risky. Explosion-proof chillers, constructed with non-sparking materials and components, minimize the risk of ignition, making them ideal for cooling applications near combustible substances.
High-Risk Environments
Environments such as offshore platforms, mining sites, or areas with a history of volatile incidents are considered high-risk zones. In such settings, using explosion-proof cooling units becomes crucial for maintaining cooling processes while safeguarding personnel and assets against potential explosions or fires.
Laboratories and Research Facilities
Laboratories and research facilities dealing with flammable solvents, chemicals, or gases need specialized cooling systems that prioritize safety. Explosion-proof cooling systems are equipped with robust safety features, including temperature monitoring and automatic shutdown systems, which ensure that any potential threats are swiftly neutralized.
Compliance with Industry Regulations
Adhering to stringent safety standards and regulations is mandatory in industries dealing with hazardous materials. Industrial chillers are specifically designed and tested to meet or exceed these industry requirements, providing organizations with the peace of mind that they are operating within compliance.
Preventing Downtime and Losses
An explosion or fire can lead to costly downtime, production halts, and damage to equipment. Investing in an explosion-proof chiller is a proactive measure that mitigates the risk of accidents, preventing unplanned shutdowns and financial losses due to safety incidents.
Cold Shot Chillers Manufactures Explosion-Proof Chillers & Cooling Equipment
When it comes to industries that require reliable and safe cooling solutions, Cold Shot Chillers stands out as a leading manufacturer of explosion-proof chillers and cooling equipment. With a strong commitment to quality and adherence to stringent safety standards, Cold Shot Chillers has established itself as a trusted name in the industry.
Cold Shot Chillers takes pride in its state-of-the-art manufacturing facilities that enable the production of high-quality explosion-proof chillers and cooling equipment. Each product is meticulously engineered and tested to meet or exceed industry safety standards, providing peace of mind to customers who rely on these critical systems for their operations.
Contact us online or call us today at 1.800.473.9178 for more information.