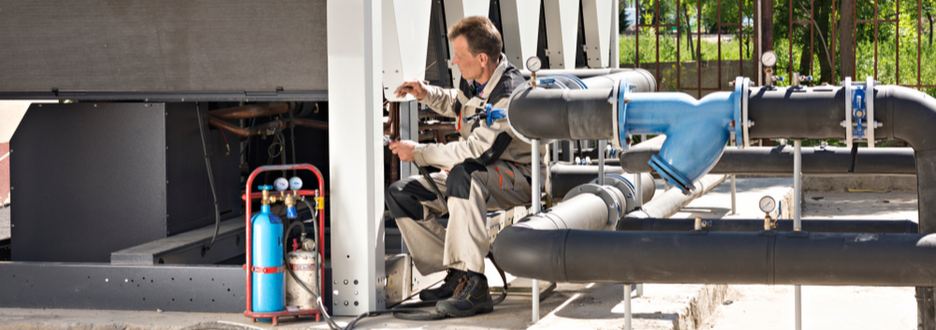
Chiller Troubleshooting Guide: Common Issues & Solutions
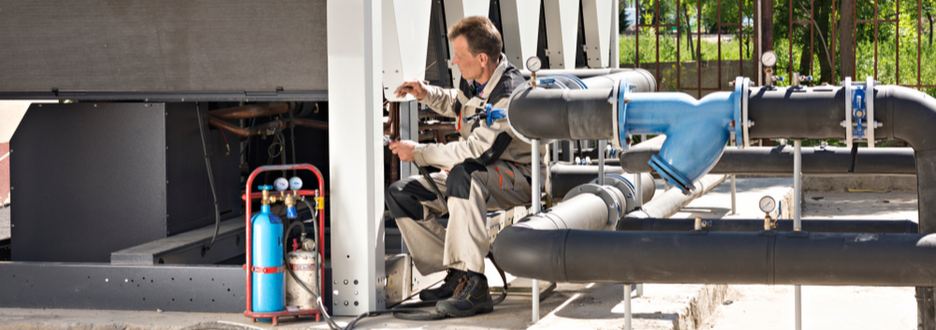
Chillers are essential for meeting the temperature requirements of several industrial processes, thus, consuming significant amounts of energy in these facilities. As a result, operators must prioritize the correct operation and maintenance approach to maximize system performance, ensure prolonged lifespan, and minimize energy costs. This article identifies common chiller problems and solutions and highlights relevant troubleshooting guidelines.
Click Here to Download Our Chiller Troubleshooting Guide Flow Chart
3 Common Causes of Chiller Problems
Incorrect operating practices, negligence to maintenance, and incorrect chiller sizing are three common causes of chiller problems. Therefore, operators must actively consider these factors to mitigate potential threats to the cooling equipment.
1. Improper Operation
Industrial chillers come with manuals containing manufacturer’s guidelines for correctly operating them. Operators must follow these guidelines as poor operating practices adversely affects equipment efficiency and lifespan. While these cooling systems may continue working regardless of improper practices, it is noteworthy that the systems become more susceptible to more severe and expensive problems. Mitigating this threat involves implementing training programs on correct chiller operation and maintenance and efficient chiller maintenance programs.
Make chiller preventive maintenance easy with the Cold Shot Guardian™ App.
2. Maintenance Neglect
Operators may disregard proper maintenance practices, which are detrimental to the overall performance of water cooled and air cooled chillers and lead to excessive energy consumption. Operators must ensure effective maintenance comprising adequate equipment diagnostics using operating logs. Moreover, chiller units require regular inspections to ascertain their conditions and schedule preventive and corrective maintenance.
3. Incorrect Sizing
Proper chiller sizing is crucial for efficient cooling in industrial facilities. An incorrectly sized unit can cause several issues:
- Undersized chillers may struggle to provide sufficient cooling, leading to inadequate airflow and system inefficiencies.
- Oversized chillers can limit low-load operation, increasing energy consumption and operating costs.
Operators should evaluate the cooling capacity of existing air cooled chillers to ensure they match the facility’s cooling demands.
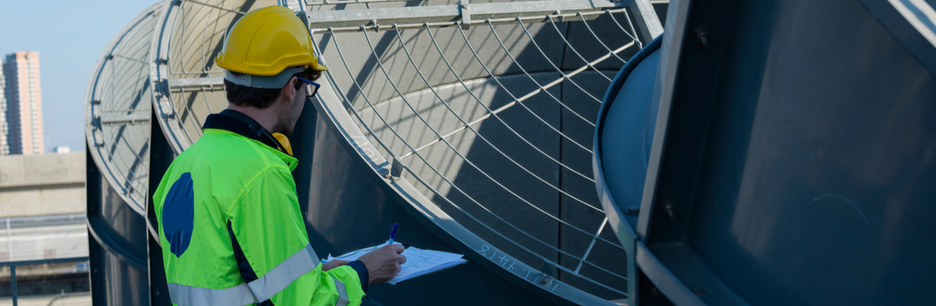
Troubleshooting Basics for Water Chillers
Air cooled and water cooled chillers remain vulnerable to damage regardless of proper operation and regular maintenance due to degradation or deterioration over time. Understanding common initial troubleshooting steps can allow operators to identify the potential issue before chiller repairs.
Chiller Won’t Start
Two common factors that can prevent chillers from starting include loose wiring and a blown fuse/circuit breaker. Moreover, a power switch in the off state may prevent the chiller from running. Operators must check the equipment for these common problems to ensure the system runs effectively.
Causes:
- Loose Wiring – Connections may have loosened over time, preventing proper electrical flow.
- Blown Fuse or Tripped Circuit Breaker – Electrical overloads can cause these safety devices to shut down the system.
- Power Switch Off – The chiller may have been inadvertently turned off or not properly restarted after maintenance.
- Control System Issues – Faulty relays, sensors, or PLC malfunctions can prevent startup.
- Low Refrigerant Pressure – If the pressure is too low, built-in safety controls may prevent operation.
Troubleshooting Steps:
- Inspect and tighten any loose electrical connections.
- Check for blown fuses or tripped breakers and replace/reset as necessary.
- Verify that the power switch is in the “on” position.
- Review error codes on the control panel to diagnose potential issues.
- Check refrigerant pressure levels and ensure they are within the required range.
If the issue persists, a technician should perform a more detailed electrical and mechanical inspection.
Insufficient Cooling
When a chiller isn’t providing adequate cooling, the issue may stem from temperature regulation failures or system inefficiencies.
Causes:
- Iced-Up Evaporator – Excess moisture or low refrigerant can cause ice buildup, reducing heat exchange.
- Degraded Coolant Fluid – Old or contaminated coolant loses efficiency and can’t properly absorb heat.
- Dirty or Blocked Condenser – Dust and debris can obstruct airflow or water flow, reducing cooling capacity.
- Incorrect Setpoints – Temperature settings that don’t align with process requirements can impact performance.
Troubleshooting Steps:
- Check the chiller outlet temperature and compare it to the setpoint.
- Inspect the evaporator for ice buildup and allow it to thaw if necessary.
- Drain and replace degraded coolant fluid with fresh, manufacturer-approved coolant.
- Clean condenser coils or ensure proper water circulation for water-cooled units.
- Adjust temperature settings to align with operational needs.
If cooling issues persist, a deeper system evaluation may be required.
Insufficient Pumping
Poor coolant flow can be caused by several factors, including low coolant volume, a partially closed valve, pump failure, or restrictions in the process line. Any of these can disrupt the refrigeration cycle and reduce the system’s efficiency. Checking these components can help identify and resolve the issue.
Causes:
- Low Coolant Volume – A shortage of coolant in the reservoir prevents proper circulation.
- Partially Closed Valves – Restricted flow due to improper valve positioning can reduce pumping efficiency.
- Pump Failure – A malfunctioning pump may struggle to circulate coolant through the system.
- Process Line Restrictions – Blockages in pipes or heat exchangers can limit flow.
Troubleshooting Steps:
- Check the coolant reservoir and refill if necessary.
- Inspect and fully open any partially closed valves.
- Listen for unusual pump noises that may indicate wear or failure.
- Flush process lines to remove potential blockages.
If coolant flow remains inadequate, a detailed inspection of the pump and piping may be needed.
Additional Chiller Problems
Manufacturers equip modern-day chiller systems with fault or error code display capabilities. These features can rapidly notify operators about prevalent conditions affecting system performance. Moreover, operators can rapidly diagnose and identify problems due to the specificity of the error codes and fault displays. Some common conditions or faults chiller systems notify operators about include:
High Temperature
The process temperature may increase above the user-set temperature value of the chiller system. This condition can trigger an alarm from the system and may result from a higher heat load than the chiller capacity. Moreover, a lower setting than standard requirements in the chiller system may also trigger the high-temperature alarm.
Causes:
- Excessive Heat Load – The chiller is trying to cool beyond its chiller capacity.
- Restricted Heat Dissipation – Dirty condensers, low water flow, or blocked airflow reduce cooling efficiency.
- Incorrect Temperature Setpoint – A setpoint too high for the process needs can trigger an alarm.
- Refrigerant Issues – Low refrigerant levels or leaks can cause poor heat absorption.
- Mechanical Failures – Malfunctioning pumps, fans, or compressors can prevent proper cooling.
Troubleshooting Steps:
- Reduce the heat load if it exceeds the chiller’s capacity.
- Clean condensers and ensure proper water or air circulation.
- Verify temperature setpoints and adjust if needed.
- Check refrigerant levels and inspect for leaks.
- Ensure pumps and fans are operating correctly.
If the problem persists, professional maintenance may be required.
Low Temperature
A process temperature below the user-set temperature value can also trigger an alarm. This condition is common with insufficient heat load or improper low-temperature alarm settings in the chiller system.
Causes:
- Insufficient Heat Load – The chiller is removing more heat than the process generates.
- Improper Setpoint Configuration – A temperature setting too low can cause unnecessary alarms.
- Faulty Temperature Sensors – Malfunctioning sensors may incorrectly detect low temperatures.
- Refrigerant Overcharge – Excess refrigerant can cause the system to overcool.
Troubleshooting Steps:
- Increase the heat load or adjust process conditions.
- Verify and adjust temperature setpoints as needed.
- Inspect and calibrate temperature sensors.
- Check refrigerant levels and adjust if necessary.
If freezing occurs, turn off the chiller and let it thaw before restarting.
Low Coolant Level
A low coolant level alarm indicates that the chiller’s coolant has dropped below the acceptable range. This can reduce heat transfer efficiency and lead to system failure if not addressed.
Causes:
- Evaporation – Over time, coolant can naturally evaporate, especially in open systems.
- Leaks – Cracked hoses, faulty seals, or worn-out fittings can cause fluid loss.
- Improper Maintenance – Failing to monitor and refill coolant levels regularly can lead to shortages.
Troubleshooting Steps:
- Inspect the system for visible leaks and repair any damaged components.
- Check hoses, seals, and fittings for signs of wear or damage.
- Refill coolant to the recommended level using the correct type.
- Monitor the system for recurring drops in coolant level.
If coolant loss continues, a professional inspection may be needed to identify hidden leaks.
Over-Temperature
An over-temperature alarm occurs when the chiller’s process temperature exceeds the set safety limit. This issue can reduce efficiency, strain components, and lead to system failure if not addressed.
Causes:
- Excessive Heat Load – The chiller is cooling more than its rated capacity.
- Poor Heat Dissipation – Dirty condensers, low airflow, or inadequate water flow reduce cooling efficiency.
- Refrigerant Issues – Low refrigerant levels or contamination can impair performance.
- Restricted Coolant Flow – Clogged filters, pump failure, or piping issues can prevent proper heat transfer.
- Faulty Sensors or Settings – Incorrect temperature setpoints or malfunctioning sensors can trigger false alarms.
Troubleshooting Steps:
- Check if the heat load exceeds the chiller’s capacity.
- Inspect condensers for dirt buildup and ensure proper airflow or water flow.
- Verify refrigerant levels and check for leaks.
- Ensure the coolant system is free of blockages and the pump is operating correctly.
- Review temperature setpoints and recalibrate sensors if needed.
Questions? Contact the Experts at Cold Shot Chillers!
At Cold Shot Chillers, we offer our clients high expertise and deliver advanced solutions for various industrial applications. Our best-in-class air-cooled and water-cooled chillers can efficiently reduce and maintain the ideal temperature for all your cooling needs. At the same time, our experts can help you adequately troubleshoot and identify prevalent chiller issues.
Contact our experts today for further information about our industrial chilling products and services.