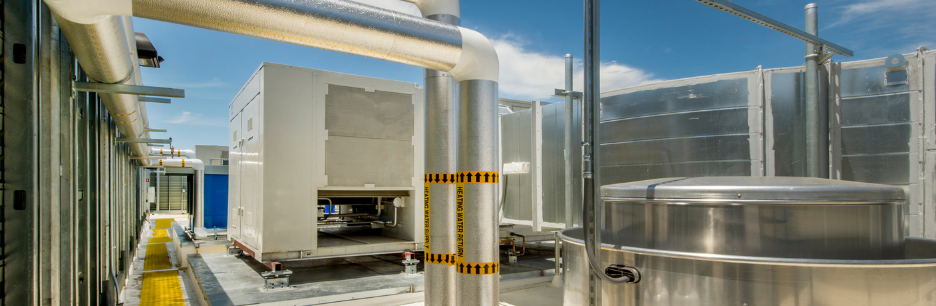
Different Types of Chillers: Industrial Chillers Guide
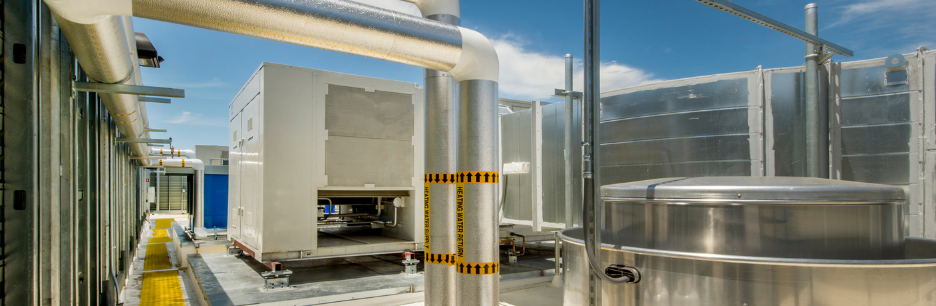
Need fast, reliable process cooling? Industrial chillers can handle it. This guide breaks down the main types and helps you find the right one for your job.
Types of Industrial Chillers (Based on Condenser Type)
The three major types of industrial chillers in use today are air-cooled, water-cooled, and evaporative condensed chillers. Let’s take a closer look at all three:
Water-Cooled Chillers
The most common types of industrial water chillers use water from an external tower to cool the gaseous refrigerant in the condenser. After expelling its heat, the refrigerant undergoes a phase change into a liquid and is recirculated into the system.
The Pros
- Water-cooled chillers are generally more efficient
- They have a quieter operation
- They are suitable for both small-scale and commercial-scale process cooling
- Portable solutions are available for facilities with space constraints
The Cons
- Water-cooled industrial chillers can be costly to install and maintain due to the additional cooling water tower, tanks, and water pump
- Since they require a constant supply of water for cooling, they might not be suitable for locations with water shortages or restrictions
- Water-cooled systems require periodic condenser water treatment to prevent the formation of mineral deposits in the system.
Explore portable, stationary, central, and custom water-cooled chillers from Cold Shot Chillers here.
Air-Cooled Chillers
Air-cooled chillers use ambient air to reject heat from the refrigerant in the condenser before condensation and recirculation. Additionally, air fans attached to the unit help speed up the cooling process.
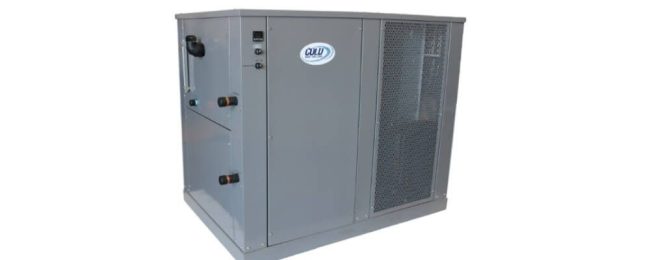
These types of industrial chillers are suitable for industrial processes where the discharged heat will not be an issue, as they tend to produce considerable warmth at the site.
The Pros
- Portable solutions are available for facilities with space constraints
- Air-cooled chillers are available for small-scale and commercial-scale cooling depending on sizing and chiller capacity
- They are cheaper to install and maintain than water-cooled systems
- The heat from the chiller can warm the facility during cold periods, providing additional cost and power savings.
The Cons
- Air-cooled industrial chillers use cooling fans that produce some level of noise
- The life expectancy can be less than that of a water-cooled chiller
Comparison Between Air-cooled & Water-cooled Chillers
While the components of air- and water-cooled chillers are mostly the same (condenser, expansion valve, evaporator, and compressor), the main difference is how the refrigerant is cooled.
In an air-cooled chiller, hot refrigerant entering the condenser is exposed to atmospheric air, rejecting the heat before it condenses to its liquid state. On the other hand, in a water-cooled unit, hot refrigerant gas is sent to a water-cooled heat exchanger or condenser, and the refrigerant is cooled using water from a cooling tower. For a better understanding, learn how cooling towers and chillers work together.
Classification of Chillers (Based on Mode of Operation)
Industrial chillers can be further grouped as “vapor compression” or “vapor absorption” types based on how the refrigerant is transported within the system. Take a closer look at how a chiller works in these different system types.
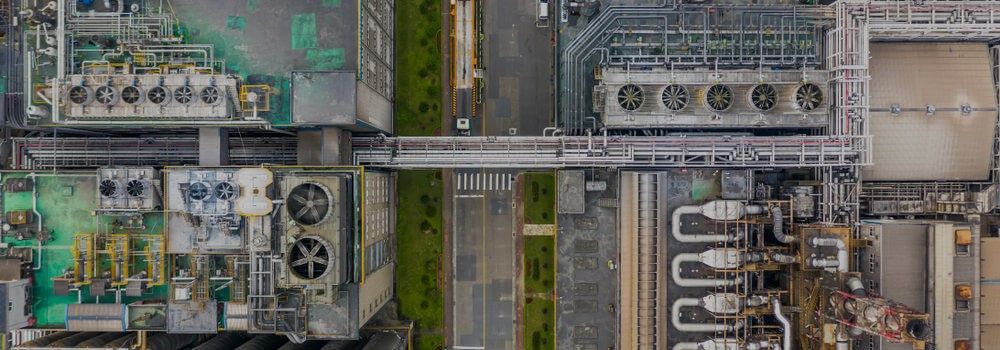
Vapor Compressor Chillers
Vapor compressor chillers use a compressor to pump refrigerant, which extracts unwanted heat from a process. The components of the system are the same as in the absorption type – we have an evaporator, a condenser, and an expansion unit. However, there is no absorbent medium in the unit.
Vapor Absorption Chillers
Unlike vapor compressor systems, vapor absorption chillers use a heat source to transport the refrigerant around the system for cooling. The components of the system are the same as in vapor compressor-type chillers, but in place of the compressor, there is an absorber, a pump, and a generator.
The heat source can be heated by water or steam; the refrigerant can be a low Global Warming Potential (GWP) type like R-134a or R1234ze, and the absorption medium can be a solution of Lithium Bromide or ammonia. The heated water or steam helps regenerate the adsorption solution.
Screw Chiller vs. Centrifugal Chiller
Centrifugal chillers use high-speed impellers to compress refrigerant and handle large cooling loads (150-6000 tons). They’re best for big facilities like airports, campuses, and large factories where full-load efficiency matters.
Screw chillers use twin rotors to move refrigerant. They’re more compact, quieter, and easier to maintain – ideal for high-rise buildings and mid-size systems.
Cold Shot Chillers recommends centrifugal chillers for large, constant loads and screw chillers for space- or noise-sensitive installs. Use our chiller sizing calculator to find the right fit.
Types of Industrial Chillers (Based on Application Type)
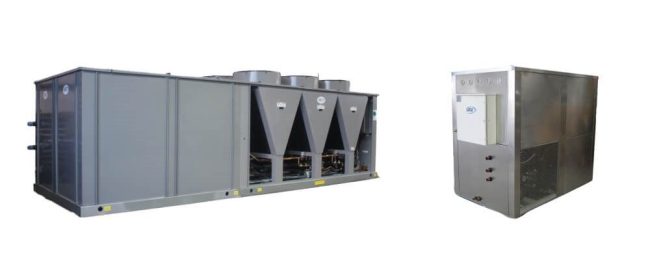
Food & Beverage Chillers
Maintaining optimal temperatures for food and beverage products is critical to ensure their safety and quality. Food and beverage chillers are used in the industry to achieve this, whether it’s to cool liquids like milk or juice or to keep food products fresh. Different types of chillers are available, including air- and water-cooled units, with the size of the chiller depending on the amount of product being cooled and temperature requirements.
Medical Chillers
Medical chillers protect heat-sensitive devices like MRI machines, CT scanners, and lab analyzers. These systems need tight temperature control 24/7 to avoid shutdowns, drift, or faulty results. Medical chillers are quiet, precise, and built for reliability. Some models also help regulate humidity for cleanroom or lab conditions.
HVAC Chillers
HVAC chillers are built to cool large-scale climate systems in buildings like hospitals, factories, and server rooms. These industrial chillers circulate chilled water or glycol through air handlers or process loops to remove heat from spaces or equipment.
Units vary from compact systems for small commercial use to multi-ton machines for major industrial cooling loads. Some are designed to handle 24/7 operation in mission-critical environments with tight temperature tolerances. Others offer modular setups that scale with demand.
Metal Finishing Chillers
Industrial chillers for metal finishing ensure high-quality metal plating and chemical processes. The precise control of temperature provided by these chillers is necessary to avoid corrosion, pitting, and other defects resulting from incorrect temperature regulation. Therefore, when selecting an industrial chiller for metal finishing, it’s important to consider factors such as the size of the application, the required temperature range, and the type of chemicals being used.
Industrial Chillers
Industrial chillers cool heavy-duty machinery and industrial processes in factories, packaging lines, and chemical plants. Designed for nonstop use, they handle high heat loads in tough conditions. Air-cooled models work well where water is limited, while water-cooled systems deliver higher efficiency. Cold Shot units are built with non-ferrous piping, stainless tanks, and industrial pumps to survive real-world shop floors.
Plastic Processing Chillers
Plastic processing chillers keep molds, extruders, and dies at stable temps to prevent defects like warping or shrinkage. Precise cooling improves product quality, reduces scrap, and speeds up cycle times. Cold Shot offers both air– and water-cooled chillers to meet specific process needs.
Cold Shot Chillers Has the Best Industrial Chillers for Your Application
For over 30 years, Cold Shot Chillers has manufactured the best industrial chiller systems to meet the process cooling needs in industrial and commercial applications nationwide.
Cold Shot Chillers offers ruggedly dependable and efficient industrial chillers with close tolerances for any application as well as parts and accessories. For inquiries, please contact us online today or call us at 1.800.473.9178.
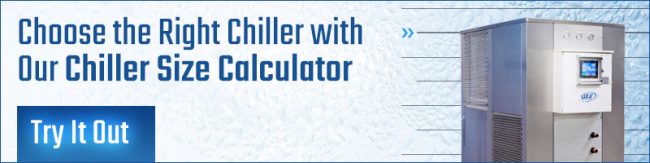