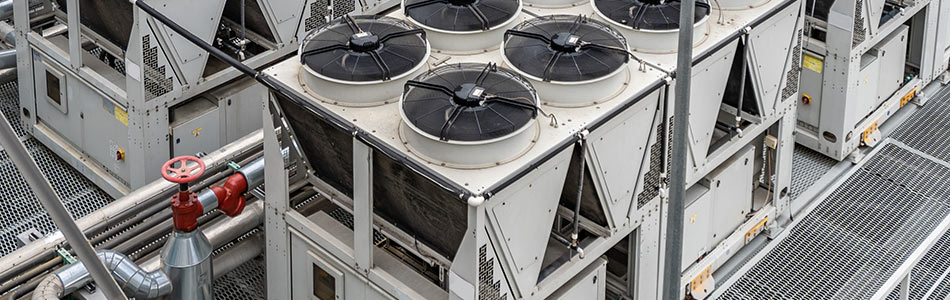
What is an Adiabatic Cooling System?
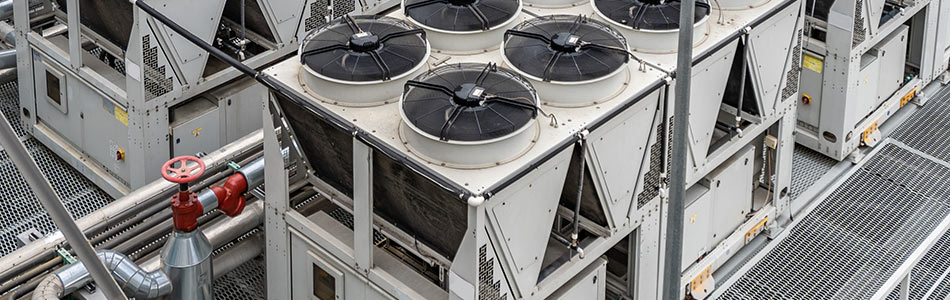
Traditionally, industrial process cooling has involved the use of massive quantities of water to dissipate the heat energy generated during manufacturing cycles. However, technology incorporating adiabatic cooling is proving to be a cost-effective and efficient way to ensure optimal process temperature regulation while reducing water and energy consumption.
This article will highlight the key advantages of operating an adiabatic cooling system.
What is Adiabatic Cooling?
Adiabatic cooling operates on the principles of thermodynamics where energy (heat) is transferred from one medium to another as “work” without an actual exchange of mass. The adiabatic cooling process occurs when a reduction in the pressure within a system causes a volume expansion, resulting in “work” on the surrounding environment.
Adiabatic cooling systems exploit this pressure-temperature relationship to provide cooling across a broad range of industrial processes.
How Do Adiabatic Cooling Systems Work?
A typical adiabatic cooling system pulls air from the external environment, reduces its temperature by evaporating water in its presence, and then feeds the cooled air to a heat exchanger. The heat exchanger eliminates heat energy from the associated process/equipment and transfers it to the cool ambient air. Once heated, the temperature of the circulating air is lowered by evaporation before a new cooling cycle.
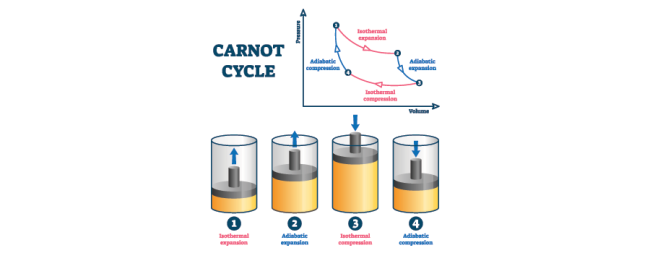
Adiabatic cooling can be one of three types:
- Direct adiabatic cooling
- Indirect/direct (two-stage) adiabatic cooling
- Indirect adiabatic cooling
Direct Adiabatic Cooling
This process, also known as wet-bulb cooling is termed direct because there is a direct interaction between water and air utilized within the system. Water is directly evaporated into a stream of heated air to facilitate its cooling. This is the most widely employed adiabatic cooling technique worldwide.
Indirect Adiabatic Cooling
In indirect adiabatic (evaporative) cooling, water is evaporated in a separate air stream that does not mix with the air intended for cooling. Heat transfer occurs at the surface of pipes within the heat exchanger. Humid evaporated air passed over the exterior of the hot air channels absorbs the heat and cools the air within them.
Indirect/Direct (Two-Stage) Adiabatic Cooling
A two-stage cooling process incorporates elements of both direct and indirect evaporative cooling methods. The first stage of the process is indirect cooling achieved by recirculating cold water in a heat exchanger to eliminate heat from ambient air. The second half of this cooling process is a direct “wet bulb” phase which further reduces the temperature of the cooling air. Bringing the air to be cooled into direct contact with the evaporating water will cause its temperatures to drop to desired levels.
Combining both direct and indirect cooling phases allows more rapid cooling to even lower temperatures than what is achieved using either method alone. Also, two-stage cooling is a very energy-efficient, cost-saving, and environmentally friendly alternative to other stand-alone adiabatic cooling techniques.
Summary of the Adiabatic Cooling Process
Adiabatic cooling of air is an indirect evaporative cooling process air flowing through a closed-loop is pre-cooled to the desired temperature. Water channeled through an adiabatic system is evaporated as required. The state change from liquid to gas results in an energy transfer in the form of heat. The thermal energy removed from the evaporated water facilitates the cooling of any associated equipment or instruments.
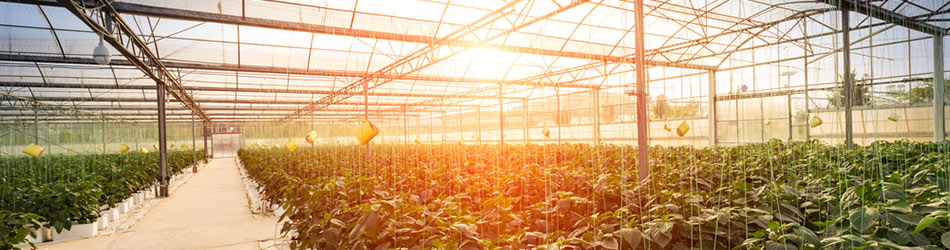
Industrial & Commercial Applications of Adiabatic Cooling
Adiabatic cooling systems are currently used in a wide range of commercial and industrial processes to maintain optimal operating temperatures. Other common applications of adiabatic cooling devices include:
- Greenhouse temperature regulation
- Residential air-conditioning
- Refrigeration systems
Adiabatic Cooling Systems for Chillers
Adiabatic cooling can be used in chiller units, replacing conventional water or air-cooled devices. Chiller systems based on adiabatic cooling may possess even greater cooling efficiency than conventional air-cooled or water-cooled devices, depending on the external environment and cooling load.
You can find more information about how chillers work on our blog.
Top Perks of Adiabatic Cooling
The key advantages of adiabatic air-cooled chillers are outlined below.
- Automated temperature controls removing the need for human operators
- Most adiabatic chiller systems have a simplified user interface making operation easier
- Significantly greater energy savings compared to other conventional cooling devices. Some evaporative chillers offer up to ninety percent on energy savings compared to other cooling units
- Lower moisture generation makes the adiabatic chiller systems ideal for moisture-sensitive equipment and processes
- Water consumption associated with evaporative cooling is significantly less than conventional water-powered cooling units
- Less concern on environmental impact as adiabatic cooling generates minimal waste with negligible effects on the immediate surroundings
- Water used in an adiabatic chiller cooling unit is in a closed loop with minimal risk of leakage, exposure to contaminants that might alter cooling efficiency
- Adiabatic cooling systems for chillers are quite effective in hot and dry environments where water is not readily available
- Adiabatic chillers are very cost-effective devices which are easy to install and operate
- Strict temperature regulation ensures an overall higher efficiency of cooling as the system is only activated intermittently.
Contact Cold Shot Chillers for Your Process Chiller Needs
Over the last three decades, Cold Shot Chillers has provided high-quality industrial cooling solutions to all our clients. With a unique approach to business, Cold Shot has carved a unique niche as one of the leading process chiller manufacturers in the US.
Please contact us for a quote or to learn more about how we can help meet your process cooling needs with our air-cooled chillers.