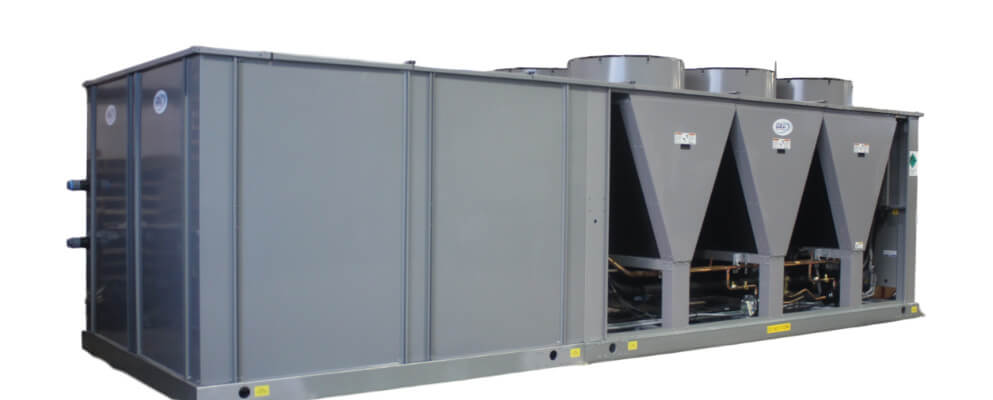
WHAT ARE CLOSED-LOOP CHILLER SYSTEMS AND HOW DO THEY WORK?
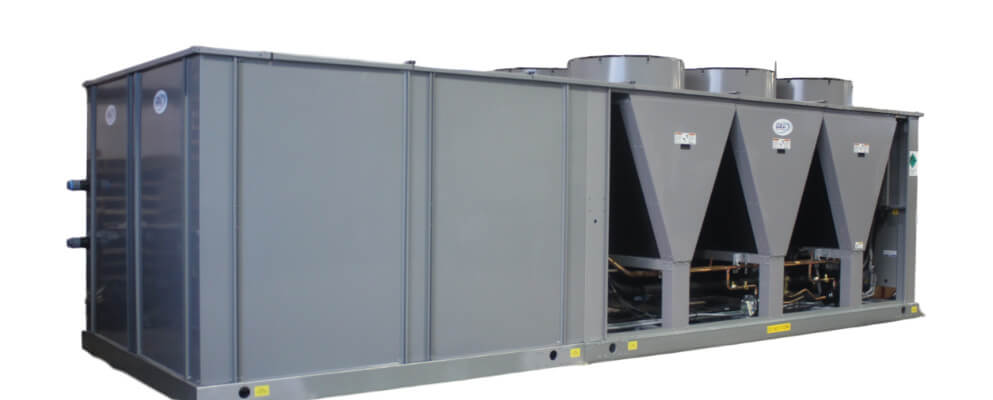
Chillers have become indispensable in a vast number of industrial processes ranging from plastic processing to applications in pharmaceutical preparations and medical diagnostics. Different types of chiller systems exist including open-loop chillers, in-line chillers, and closed-loop chillers. In this article, we will be focusing on the closed-loop chiller system.
What Are Closed-Loop Chillers?
Closed-loop chillers are recirculating systems that employ the use of coolant fluid in a closed-loop setup to exchange heat from various industrial and commercial processes.
The coolant used in a closed-loop chiller can include:
- Water and water-based coolants (de-ionized water, water/glycol mix, water-based synthetic coolants)
- Oil and oil-based coolants
So, how does a chiller work with these refrigerants in a closed loop?
How Do Closed-Loop Chiller Systems Work?
The coolant is chilled in a coolant tank and repeatedly passed through a heat load where it absorbs heat from industrial processes or equipment. The heat absorbed from the heat load is then dissipated in an evaporator before returning to the coolant tank for re-cooling and recycling through the closed-loop.
The temperature of the coolant is regulated by a thermostat that automatically detects changes in the temperature within the coolant tank. This thermal controller then adjusts the refrigeration effect in the evaporator accordingly to ensure the fluid in the coolant tank is at an optimal temperature for its next interaction with the heat load.
Benefits of Closed-Loop Water Chiller Systems
Employing a closed-loop water chiller system is not only a financially sound decision but also an environmentally-friendly one. Compared to a single pass cooling setup which uses water only once before dumping, a closed-loop water chiller and cooling tower will recycle water through a closed-loop repeatedly.
A closed system has several advantages such as:
- reduction in the amount of water used for cooling
- lower sewer usage costs
- limitation of the release of contaminants into water bodies which may be harmful to aquatic life
- provision of significant returns on investment over time
Minimizes Water Consumption
With its sealed design and cyclical mechanism of operation, a closed-loop water chiller requires very little water requirements once it has been set up. Negligible volumes of water are only lost during maintenance of components with cumulative fluid losses amounting to just a few gallons yearly.
Minimizes Environmental Contamination
Moreover, a closed-loop chiller system virtually eliminates the chances of environmental contamination as it is completely sealed. Impurities like mud, dust and biological contaminants (algae, bacterial growth) that reduce the efficiency of a typical open-loop chiller will not affect a closed-loop system. Additionally, a closed-loop chiller will work at optimal conditions for a longer period with minimal maintenance needs.
Lowers Costs of Wastewater Treatment and Disposal
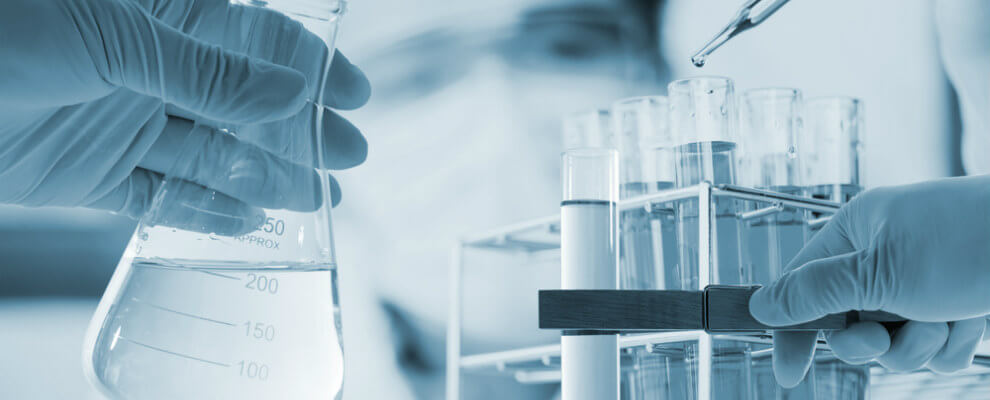
Repeated recycling of water and cooling fluids allows industries to comply with local environmental laws while cutting down on wastewater disposal costs.
Depending on local regulations, the disposal of used water and other effluents from a chiller system may cause companies to spend significant finances on treatment costs. Some municipalities will only allow wastewater to be discharged into environmental water bodies after extensive checks and treatments the cost of which will be borne by the company producing the waste.
Further, local authorities may impose stringent taxes on industries producing wastewater. These additional costs can be avoided by simply recirculating coolants and water in a closed-loop system.
Ensures Precise Temperature Regulation and Improved Cooling Efficiency
Closed-loop cooling systems are able to maintain constant temperatures of their coolant, which provide the heat loads they interact with, the ability to precisely maintain the optimal thermal conditions vital to their operations.
Utilizing closed-loop chiller systems that are custom-built for specific industrial applications will improve the entire production process. This precise temperature regulation is advantageous and provides heat-sensitive equipment with adequate thermal protection while allowing constant reproduction of satisfactory results.
Provides Space and Operational Energy Savings
When compared to open-loop chiller systems, closed-loop cooling systems are space-efficient, as they do not require a separate heat exchanger unit. As a result, these machines will consume fewer square feet of floor space. The freed-up space can be used to store other equipment equally vital to industrial processes.
Moreover, closed-loop chillers have pumps which allow for variations in speeds depending on cooling needs. When a reduction in the temperature of the heat load is detected, the pump will work at a slower speed, thereby decreasing consumed energy and improving efficiency. This flexibility will also contribute to reducing operational costs.
Cold Shot Chillers Has the Closed-Loop Chiller You Need!
For over 30 years, the team of industrial chiller manufacturers at Cold Shot Chillers has provided high-quality chiller systems for a wide range of industries like breweries, wineries, medical facilities, food processing plants to name a few. With our experienced and dedicated support staff, we are strategically positioned to assist you with all your process cooling needs.
You can find a broad selection of water-cooled chillers and air-cooled chillers for reliable cooling on our website.
To learn more about how we can help with your process cooling needs, please contact us online today!
