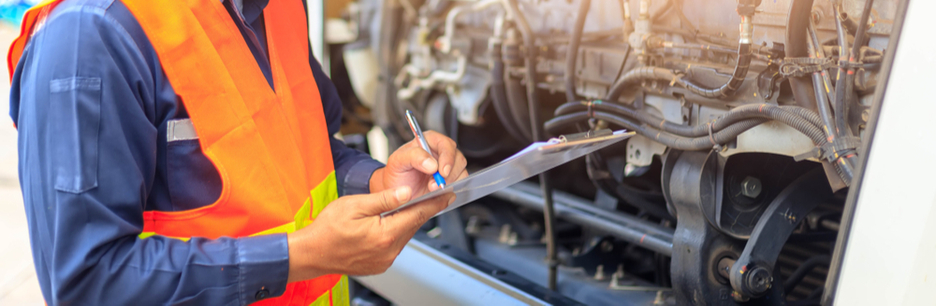
THE ROLE OF FILTRATION IN WATER CHILLERS
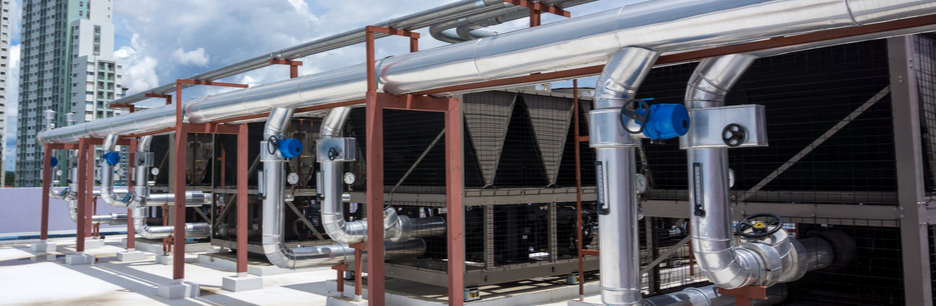
Several industrial manufacturing processes use industrial water chillers to moderate their process temperatures, boost efficiency, and maximize output. Furthermore, these chillers utilize coolant fluid to achieve effective thermoregulation. However, these process cooling fluids are prone to contamination during use, making the integration of filtration units essential.
Regardless of the industry or specific industrial application, clogs result in inefficient systems. This is no different for water chillers, cooling towers, and other heat exchangers. Let’s discuss what you need to know about filtration and water chillers.
Why Efficiency Is Important for Water Chillers
Every plant operator or process manager should plan and execute industrial processes that maximize productivity while minimizing waste. This principle of efficiency applies to the operation of industrial water chillers as well.
A water chiller is a cost-effective device that can rapidly cool large process plants. However, the presence of solid contaminants in its coolant fluids will lower the efficiency of the cooling process. In addition, a build-up of impurities can lead to a coolant channel obstruction. Therefore, contaminated chiller fluid will diminish the chiller’s cooling capacity or even shut down the process entirely.
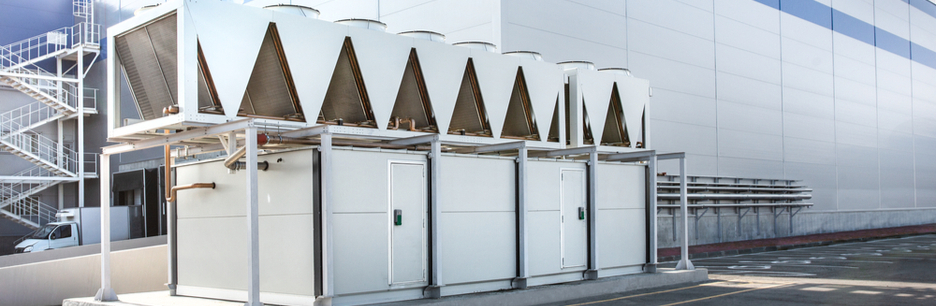
To avoid a reduction in chiller efficiency, costly equipment repairs, and avoidable downtimes, industrial operators must invest in appropriate water filtration units. Proper filtration of water chiller fluids will ensure the cooling systems retain their ability to efficiently dissipate large volumes of heat from the industrial processes they serve.
How Heat Exchangers Get Clogged
Water chillers utilize coolant to achieve process thermoregulation. In many cases, water or a mixture of water and glycol might be used. The water circulating through industrial chillers is often sourced from natural sources, including rivers, lakes, and other nearby bodies of water.
The water being harnessed is often contaminated with solid impurities such as sand and other particulate matter. So, using unfiltered water from these sources is a bad idea as it will lead to rapid clogging of the heat exchanger tubing.
Furthermore, filtered water circulating through a heat exchanger is still prone to contamination, and channel clogging is possible. Pipe corrosion and particle build-up contribute to heat exchanger clogging that can diminish cooling efficiency, leading to significant equipment damage and costly downtime.
Filtration Solutions and Maintenance Tips
Selecting an appropriate and effective water chiller filtration system is integral to optimized industrial productivity. Before choosing a chiller filtration system, plant managers should consider various factors related to their cooling requirements.
Important Considerations for Filtration Units
- The source of the coolant fluid
- The nature of contaminants in the fluid
- Temperature and pressure levels within the processing system
- Permitted downtime for maintenance
- Costs of filter unit installation and maintenance
The Source of The Coolant Fluid
Water chiller coolant sources from natural bodies of water will require sturdy filtration units. In addition, they will likely be equipped with specialized strainers and coalescers designed to handle a high volume of impurities.
The Nature of Contaminants in The Fluid
Water chiller efficiency is affected mainly by the nature of fluid used as the coolant. For example, chiller fluids might contain organic or inorganic solid contaminants that may require different filter configurations. In addition, larger particles imply a more elaborate filtration system to optimize the particle separation process.
Temperature and Pressure Levels Within the Process System
Process temperatures typically differ across industrial manufacturing systems. A processing system with higher temperature and pressure levels will require a larger chiller and more extensive filtration system.
Permittable Downtime for Maintenance
When selecting an industrial water chiller filtration system, operators must determine the amount of maintenance downtime that is acceptable. Before installing a system, plant managers should ensure that the manufacturer’s maintenance recommendations will not hurt the smooth running of their processes.
Costs of Filter Unit Installation and Maintenance
For every industrial equipment purchase, the short-term and long-term cost implications must be duly considered. Filtration water chillers are not an exception. Therefore, you should carefully consider the immediate benefits of installation and the long-term operational/maintenance expenses.
Maintenance Tips for Filtration Solutions
Industrial operators will find it helpful to schedule routine filtration equipment maintenance. Component checks, repairs, and replacements can be conducted monthly, quarterly, or yearly. The frequency will depend on the nature of the filtration equipment and the kind of contaminants they handle. In most cases, creating and keeping an industrial chiller maintenance checklist will ensure all maintenance is up-to-date. Â
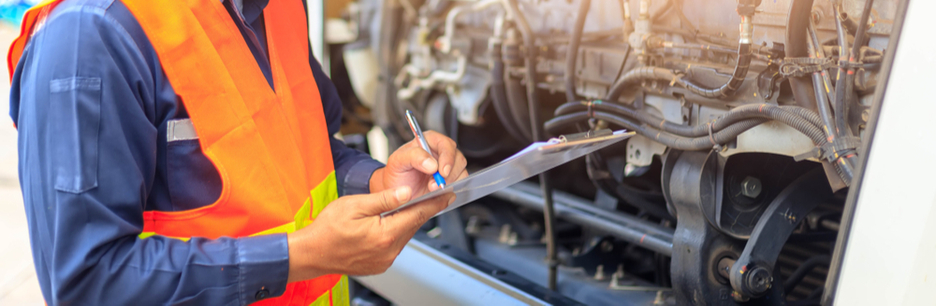
Partnering with the Right Industrial Chiller Manufacturer
The use of an effective filtration system can be used to boost overall water chiller efficiency. Partnering with a trusted chiller manufacturer will improve the efficiency of your process and give your business a competitive edge in today’s manufacturing marketplace.
At Cold Shot Chillers, we manufacture dependable water-cooled chillers, air-cooled chillers, and different types of chillers suitable for various industries. We aim to help you achieve maximum productivity by offering excellent industrial cooling solutions.
To learn more about our products and services, please contact us today!
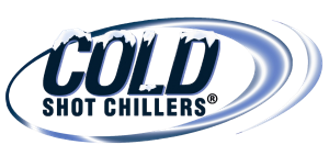