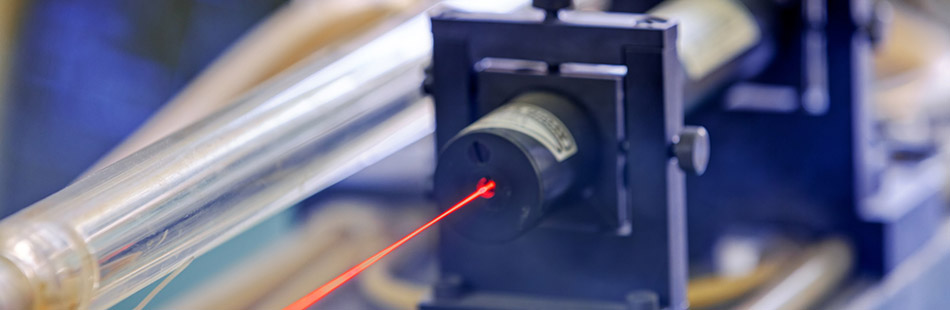
HOW ARE LASERS MADE? – LASER GENERATION PROCESSING & COOLING NEEDS
Light amplification by stimulated emission of radiation (LASER) has remained a ground-breaking technological invention since its discovery and first use. Over the years, laser beam technology has been modified and refined for use across a broad range of applications including industrial manufacturing, health, research, and communication tech.
This article covers how a laser beam is generated as well as how a laser tube can be efficiently cooled.
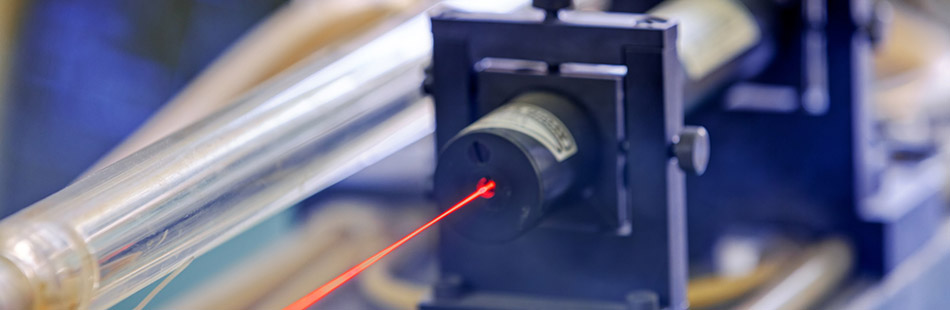
What Is a Laser?
A laser is a device that stimulates subatomic particles (electrons) to emit electromagnetic radiation. Lasers typically produce a narrow beam of light that exhibits a physical property called “coherence.” This allows laser light to be focused on a spot making it quite useful in applications such as photolithography and laser-cutting.
Industrial Application of Lasers
Laser technology has become an almost indispensable tool in numerous industrial processes today. Industries that use one or more forms of lasers are outlined below:
- Laser marking, and drilling
- Laser cladding
- Photolithography
- Laser cutting, and welding
- Fiber optics
- LED, smartphone and computer screens manufacturing
- Laser surveying systems
- Engraving
- Laser bonding
- 3D laser scanning
- Laser printing
- Plastic welding
- Additive manufacture
Dependent on the type of industrial process involved, lasers with different optical power ratings can be used.
Material processing such as soldering and sheet metal welding can be achieved using lasers with a power rating above 1 kilowatt.
Micro-material processing for smartphones, computers and LED TV screens is done using lasers with power all under 1 kilowatt.
How Are Lasers Made?
Regardless of the type of laser being utilized, the laser generation process is always similar.
To generate a laser beam, the device must possess:
- A collection of atoms in a liquid, solid or gaseous state that can be stimulated to absorb energy.
- A means of stimulating the excitable portions of theses atoms (electrons)
The laser production principle requires the introduction of energy in the form of an electric pulse into a laser cavity. This produces photon energy, which is rapidly absorbed by the electrons present within, causing them to perform a quantum leap and jump to a higher energy state. This activity is transient occurring in a matter of milliseconds with the electrons rapidly returning to their base energy state.
Simultaneously, electrons returning to base energy levels will emit photons of light that can equally go on to stimulate other electrons in their base state thus replicating and further amplifying the initial reaction.
Laser devices usually incorporate mirrors within a laser tube that help sustain a steady stream of photons while producing a concentrated laser beam.
Why Do Lasers Produce Heat?
After learning how to generate laser beams, it is clear that the production of light energy is always associated with some degree of heat generation. Considering that laser light is an amplified form of light energy, it follows that the amount of heat generated during its creation will be significantly higher.
Industrial laser devices generate enormous amounts of heat that can cause damage to the material being worked on as well as the laser components themselves. As a result, industrial laser operators must ensure they maintain their devices within optimal temperature ranges by using an associated cooling device.
Optimal CO2 Laser Temperatures
Operating CO2 lasers at high temperatures will diminish their accuracy, and stability. The increased thermal stress will damage laser components resulting in costly repairs or outright equipment replacement. Also, exposing sensitive materials to uncontrolled laser temperatures will alter the manufacturing process resulting in defective final products.
Most industrial CO2 lasers can be safely and efficiently operated within the temperature range of 59 °F to 77 °F.
How to Maintain a Healthy CO2 Laser Tube
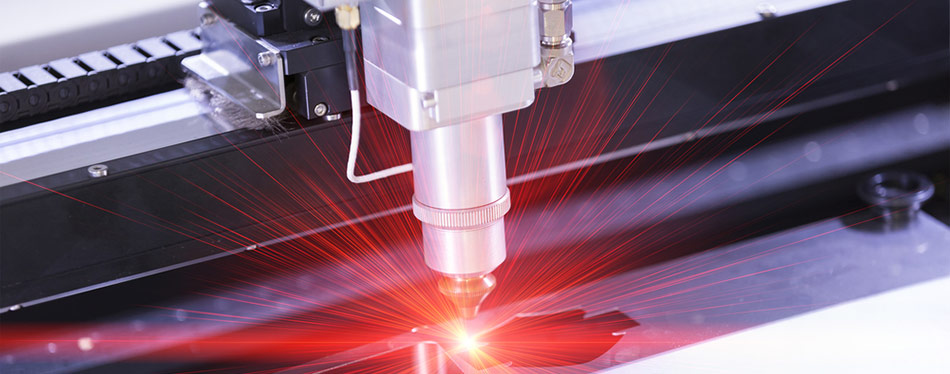
The most effective way to maintain your CO2 laser operating efficiently for as long as possible is to incorporate a laser chiller device. These industrial water chillers will provide the thermoregulation required to prevent component breakdown or product damage, by eliminating excess heat energy produced during laser operation.
How Do Industrial Laser Chillers Work?
So, how do chillers work to keep your laser technology stable?
Standard laser water chillers possess a refrigeration unit that channels coolant to the process laser tube where heat exchange occurs cooling the laser to optimal temperatures. The heated cooling fluid is returned via piping to the refrigeration unit where the absorbed heat is eliminated thus regenerating the coolant for a new cycle of heat exchange with the laser device.
Most industrial laser chiller manufacturers offer units between 600 watts to several kilowatts in capacity.
What to Consider When Purchasing a Laser Chiller
Some key factors to consider when deciding on a choice of a laser chiller unit include:
- The power rating of the laser vs. chiller capacity
- Cost of purchase and installation
- Specific cooling needs of various laser
- Additional laser features
Maintain Your CO2 Laser Cutting Temperature with Cold Shot Chillers
At Cold Shot Chillers, we manufacture and install high-quality process chillers compatible with a broad range of industrial processes. Our custom-built laser chillers are designed to provide optimal temperature regulation for all your laser cutting operations.
Contact us today for detailed chiller specifications or a quote on our air-cooled chillers or water-cooled industrial chillers.
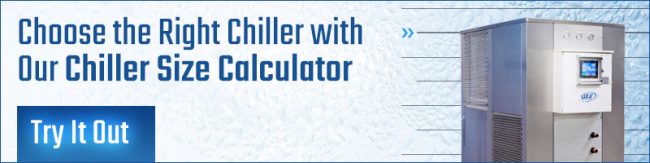