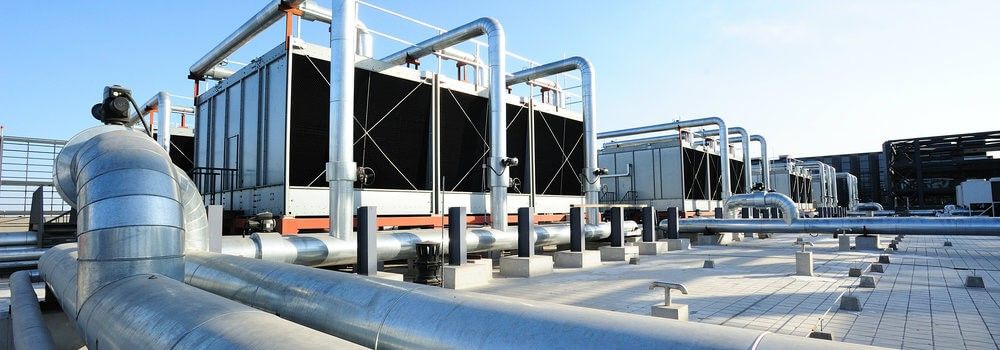
What is a Chiller & How Does it Work?

If your facility uses process fluids or heavy-duty machinery that generates heat, you’ll need an industrial chiller system to cool your processes and internal machine components. Understanding how an industrial chiller works and the various types of chillers available will help you choose the right cooling needs.
What is a Chiller?
An industrial chiller is a refrigeration system used to lower the temperature of machinery, industrial spaces, and process fluids by removing heat from the system and transferring it elsewhere. Industrial chillers are essential for temperature regulation in several industrial processes, such as injection molding, metal plating, oilfield production, and food processing.
Why Use a Chiller?
Air-cooled chillers and water-cooled chillers alike are beneficial for industrial processes where strict operational temperatures are required. When integrated with heat-sensitive processes, chillers will prevent thermal damage to process equipment and ensure no alterations to the final products from exposure to unsuitable temperatures.
Working Principles
Industrial chillers work based on the following principles of operation.
- Phase Change: When heated, a liquid coolant undergoes a phase change into a gas, and when the gaseous coolant is supercooled, it condenses back into a liquid.
- Heat Flow: Heat energy always flows from an area of high concentration to an area of lower concentration.
- Boiling Point: Reducing the pressure over a liquid decreases its boiling point, and increasing the pressure increases its boiling point.
How Does a Chiller Work?
So, exactly how does a chiller work? An industrial chiller system is driven by one of two operational principles: heat absorption and vapor compression.
Heat absorption chillers integrate heat exchangers that pull heat away from any associated processes and dissipate them exteriorly. Heat exchangers typically comprise piping containing coolant fluids (air, water, or a mixture of water and other liquids).
Vapor compression chillers achieve a cooling effect by circulating coolant in pipes through the processes requiring cooling. This will pull heat from any associated processes into the coolant, which is then circulated to a refrigerant system that cools the chiller fluid and prepares it for a new cycle of process cooling.
Chillers consist of four key components: an evaporator, a compressor, a condenser, and an expansion unit. In addition, every chiller system contains a refrigerant.
The process starts with a low-pressure refrigerant entering the evaporator. Inside the evaporator, the chiller refrigerant is heated, causing it to undergo a phase change into a gas. Next, the gaseous refrigerant goes into the compressor, which increases its pressure.
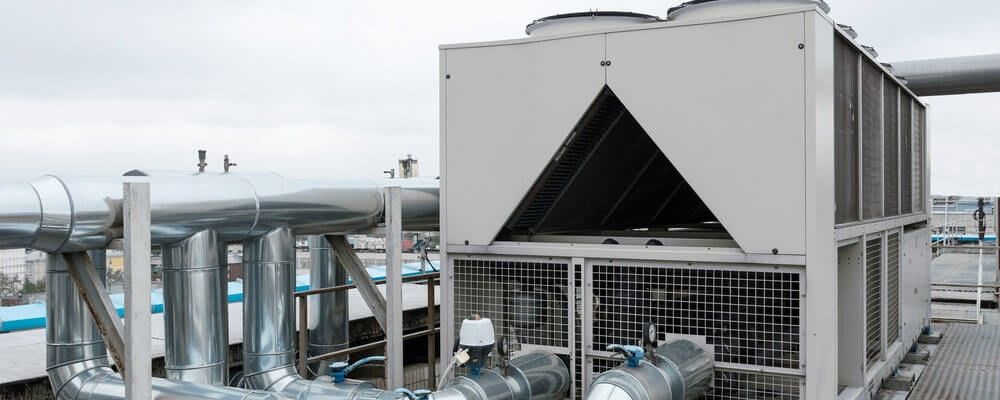
The high-pressure refrigerant goes to the condenser, which rejects the heat using cooling water from a cooling tower or ambient air from the surroundings, condensing it into a high-pressure liquid. The condensed refrigerant then goes to the expansion unit, which has a valve that acts as a metering device to limit refrigerant flow. Learn about new chiller refrigerants.
Consequently, this lowers the pressure of the refrigerant and begins the cooling process again. The entire process is known as the refrigeration cycle.
Basic Chiller Components
The central chiller components include the following:
- Condenser
- Compressor
- Evaporator
- Expansion valves
- Power unit
- Control unit
- Water boxes
Condenser
The function of a chiller condenser unit is to eliminate heat from the refrigerant being circulated through the chiller unit. This is achieved by circulating water between a cooling tower and the condenser for water-cooled variants or blowing cool air over condenser piping for air-cooled chiller units.
Compressor
The compressor is the driving unit of any chiller system. It generates the pressure gradient necessary to push refrigerant around the chiller unit to achieve process cooling. Various condensers are available, with the most popular types including centrifugal, screw, and reciprocating compressors.
Evaporators
An evaporator is placed between the expansion valve, and the condenser removes heat from any associated process into circulating refrigerant. Depending on the chiller configuration, this is then channeled to a cooling tower or air-cooled.
Thermal Expansion Valves
Thermal expansion valves between the compressor and the evaporator expand refrigerant passing through them. This action diminishes the pressure and improves the heat elimination from the evaporator.
Power Unit
All air-cooled chillers and water-cooled chillers incorporates a power unit that controls electrical energy flowing through the system. Power unit components usually include starters, power monitoring panels, and circuit breakers.
Control Panels
Control panels serve to regulate the entire cooling operation process. They usually integrate sensors, alarms, and display screens that allow operators to adjust system settings for optimal thermal control.
Water Boxes
These devices may be mounted on the chiller system evaporator or its water-cooled condenser. Their purpose is to conduct water flow effectively.
Types of Industrial Chillers
The three main types of chillers in use today are air-cooled chillers, water-cooled chillers, and absorption chillers. We will also briefly touch on cooling towers (an alternative or supplemental cooling system) and special chillers like glycol and centrifugal.
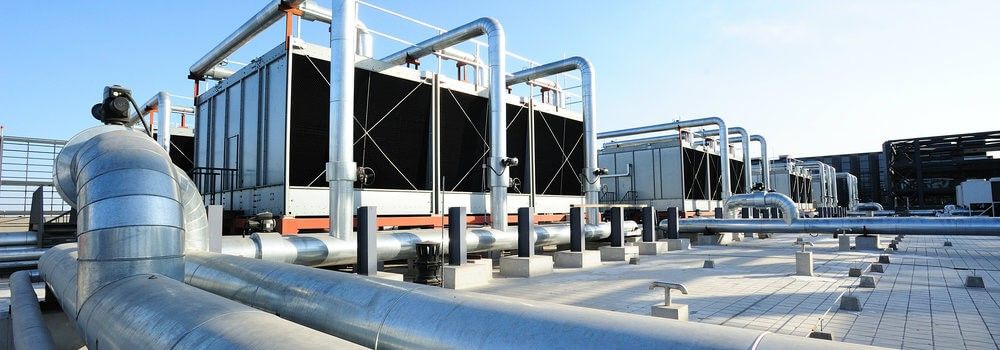
Selecting the right chiller for your industrial application will help you save costs, reduce downtime, and improve operational efficiency.
Water-Cooled Chillers
Water-cooled chillers use water from an external cooling tower to reject heat from a gaseous refrigerant in the condenser before it changes into a liquid.
Air-Cooled Chillers
In place of the cooling water, air-cooled chillers use ambient air to reject heat from the refrigerant in the condenser. Learn more about air-cooled chillers vs. water-cooled chillers.
Vapor Compressor Chillers
This type of chiller uses refrigerants to cool process fluids and spaces. A compressor is used as the driving force to pump refrigerant around the system.
Vapor Absorption Chillers
Vapor absorption chillers have no compressor in the unit. Instead, they use a heat source, e.g. solar energy or waste heat to drive the coolant through the system.
How does an absorption chiller work?
The process starts with liquid coolant in an evaporator, which turns it into gaseous form. Next, the gaseous coolant is absorbed by a concentrated absorbent such as Lithium Bromide or Ammonia, provided by a generator. Finally, the diluted solution absorbs the coolant while the cooling water absorbs heat.
The diluted solution of coolant and absorbent flows through a heat exchanger to the generator, where it is heated. The coolant vaporizes out of the solution, condenses, and is sent out for cooling again. The now-concentrated absorbent is recycled as well.
Glycol Chillers
Glycol chillers are special types that use propylene glycol, an anti-freeze, in the system. They are widely used in food-grade applications such as in the production of alcohol and for brewery chilling systems.
How does a glycol chiller work?
The mode of operation of glycol chillers is the same as that of standard air and water-cooled chillers.
Centrifugal chillers
Centrifugal chillers consist of the usual evaporator, compressor, condenser, and expansion device set-up but with additional rotating impellers which compress the refrigerant and transport it around the system. They benefit medium to large-scale cooling operations (from 150 – 6000 tons of refrigeration).
Uses of Industrial Chillers
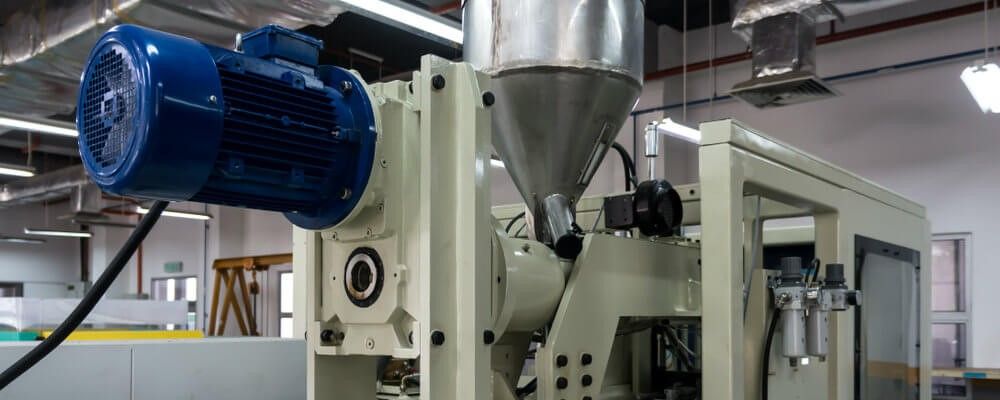
Water-cooled chillers and air-cooled chillers can be used for cooling operations in diverse industries. Below are some of the most common industrial processes:
- Food Processing – Industrial chillers are used extensively in food production and processing operations, which require a high degree of precision in temperature control. For instance, winery chillers are used for temperature control during the fermentation and storage of wine. Likewise, bakery chillers help with mixer cooling, potable water cooling, and cooling jacketed tanks of yeast, which are all critical bakery components.
- Metal Finishing – Temperature control is essential in metal finishing processes such as electroplating or electroless plating to remove the excess heat, as they typically require very high temperatures (several hundred degrees) to bond the metals. Some industries use metal-finishing chillers to cool the anodizing liquid in a heat exchanger or use glycol/water as a cooling medium to lower the temperature inside the tank.
- Injection Molding – Injection molding is a mass-production technique for creating plastic parts using an injection molding machine, thermoplastic pellets, and a mold. The process and melt must be maintained within precise temperature limits to prevent problems such as cracks, warping, and internal stresses in the final product. An injection molding chiller can supply a stream of supercooled fluid to cool the mold at an ideal rate to ensure optimum product quality.
- Space Cooling – In manufacturing plants that generate a lot of heat from heavy-duty process equipment, water-cooled chillers and air-cooled chillers can help prevent temperature extremes in offices and other working spaces. They also help save costs on purchasing separate HVAC systems for cooling.
Determining the Right Size of Chiller for Your Needs
An adequately sized chiller is critical for efficient and cost-effective processes, machinery, and space cooling. Cold Shot Chillers’ easy-to-use sizing tool can help you quickly determine your optimal chiller capacity, tonnage, and size.
Getting The Most Out of Your Chiller
The cost of installing and operating air-cooled and water-cooled chillers can be pretty high. Chiller units must be run as efficiently as possible to avoid additional charges during routine operations. Scheduling and conducting proper maintenance regularly for your system will prevent costly chiller repairs in the long term. Applicable chiller maintenance should include condenser coil inspection and cleaning, condenser water, and refrigerant maintenance. Real-time monitoring apps like Cold Shot Guardian® can be used to monitor equipment, predict system failures, and suggest pre-emptive interventions.
Trust Cold Shot Chillers for All Your Chiller Needs!
With over three decades of expertise in manufacturing air-cooled chillers and water-cooled chillers, Cold Shot Chillers provides cooling equipment and expertise for the most challenging process cooling needs.
Contact us online or call us at 1.800.473.9178 for more information about our commercial chillers and chiller parts.