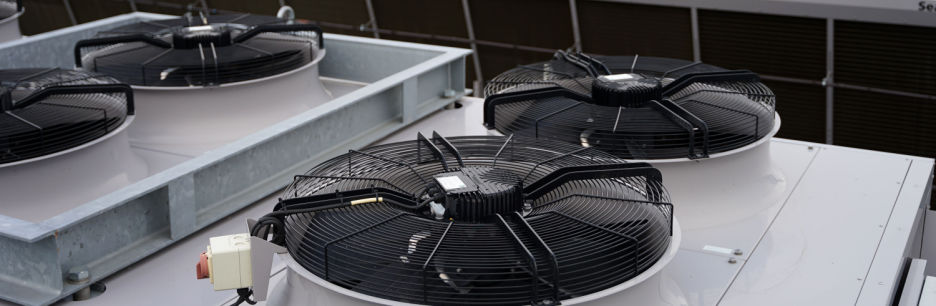
WHAT IS A DRY COOLER & WHAT ARE THE DIFFERENCES BETWEEN DRY COOLERS VS. CHILLER SYSTEMS?
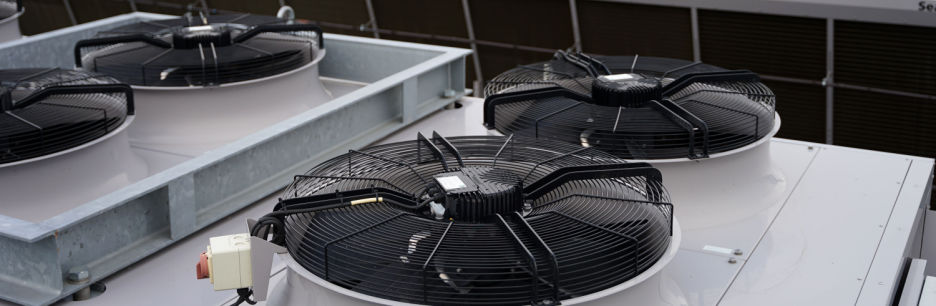
Depending on operator preference, there are different approaches to industrial cooling. While some process temperatures can be optimally maintained using conventionalĀ industrial chillers, others require alternative equipment like dry coolers.
Both thermoregulatory tools achieve a similar effect, but their mechanisms operate differently. This article will highlight the differences between a dry cooler vs. chiller and help you decide which is best for your cooling needs.
What Is a Dry Cooler?
A dry cooler is a cooling device that uses air to regulate process temperature. The cooling done by a dry cooling system is based on the principles of sensible heat rejection. A typical unit requires a cooling medium channeled from an associated process that enters a dry cooler and exchanges accumulated heat with the air circulating within.
Dry coolers have fans that pull air from the coolerās exterior to sustain the heat exchange process. A suitable temperature difference between the cooling medium and the air within the dry cooling system must be maintained to ensure efficient process cooling. A minimum difference of 5°C is usually enough.
Dry coolers are often used in applications where water is scarce or where the use of water is prohibited due to environmental regulations. They are also commonly used in industrial processes, such as power generation and chemical processing, where cooling is required to maintain optimal operating conditions.
Dry Cooler vs. Fluid Cooler
A dry cooler is essentially a fluid cooler that uses air, a relatively dry, non-liquid fluid, to accomplish process cooling. Fluid coolers more accurately refer to cooling equipment that uses fluids (liquid or gas) to regulate process temperatures.
Dry Coolers vs. Chillers
Dry coolers and chillers can be used in similar process applications to attain optimal temperatures. However, like the differences between aĀ chiller vs. heat exchanger, there are significant differences in how dry coolers and chillers function. Nevertheless, each device offers advantages when used under the appropriate conditions.
For a dry cooling system, the thermal exchange is performed by pulling in external air and circulating it over tubes containing a cooling fluid (typically water or water-glycolĀ mixture). Next, the cooled fluid is circulated through a heat exchanger attached to an associated process. The excess heat transferred to the cooling fluid is then returned to the dry cooler, and the cycle is restarted. It is important to note that a dry cooler does not have a standard refrigeration unit that chills a circulatingĀ refrigerant. Instead, it uses fans to pull in ambient air to cool its heated fluid medium.
On the other hand, industrial chillers incorporate refrigeration units (often in conjunction with heat exchangers) in their cooling setup. Chillers useĀ coolant/chiller fluid that may be cooled by air or water in their condenser. This is the basis for the differentiation intoĀ water-cooled and air-cooled chiller variants.
Dry Cooler System Design
A typical dry cooling system is designed as a dual-unit system comprised of outdoor and indoor aspects linked by a fluid pump.
The outdoor component is the dry cooler, whereas the indoor unit is made up of the following parts enclosed together:
- Compressor
- Heat exchanger
- Pipes circulating cooling fluid
- Evaporator
Pros of Using a Dry Cooler:
The advantages of opting for a dry air cooler include the following:
- Easy installation and start-up
- Overall low operating costs after initial installation
- Convenient separation of components allows operators to save vital floor space for other equipment
- Dry coolers do not require a constant water supply; therefore, supply and disposal concerns are non-existent
- Dry coolers can be programmed to operate year-round, even in environments with low temperatures
- The generated heat can be channeled directly into other processes, reducing energy waste and improving overall efficiency
Cons of Using a Dry Cooler:
- Regular monitoring (or an automatedĀ chiller monitoring system) is required to ensure cooling fluid levels do not drop below the required levels
- Additional costs of add-on components increase the total setup expenditure
Chiller System Design
Standard chiller units are designed to work on two principles: vapor compression or heat absorption with similar components.
- Compressor
- Heat exchanger
- Tubing and condenser
- Evaporator
Pros of Using a Chiller Unit:
The benefits of installing anĀ air-cooled chillerĀ orĀ water-cooled chillerĀ in a process setup are listed below:
- More precise temperature control
- Lower leaving temperature capabilities
- Operating costs are typically low after installation
- Process chillers have a high safety rating if proper routine maintenance is performed
- Chiller units are typically sturdy and have a long lifespan
- Process chillers are energy efficient
Cons of Using a Chiller Unit:
- Chiller maintenance, including the replacement of faulty components, are costlyĀ Ā
- The initial setup costs for an industrial process chiller are usually high
Cold Shot Chillers is Your Trusted Chiller Manufacturer
Cold Shot Chillers is your go-to source for reliable industrial chillers. With over 30 years of experience in the industry, we have the knowledge and expertise to provide you with top-notch chillers that will meet your needs. We offer a variety ofĀ chiller typesĀ and sizes designed to meet any application or budget requirements. In addition, our team is available to answer any questions or concerns about our products and services.
Contact us todayĀ to learn how we can help with your process cooling needs.
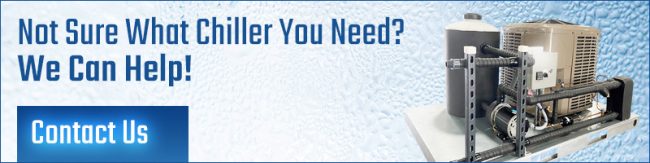