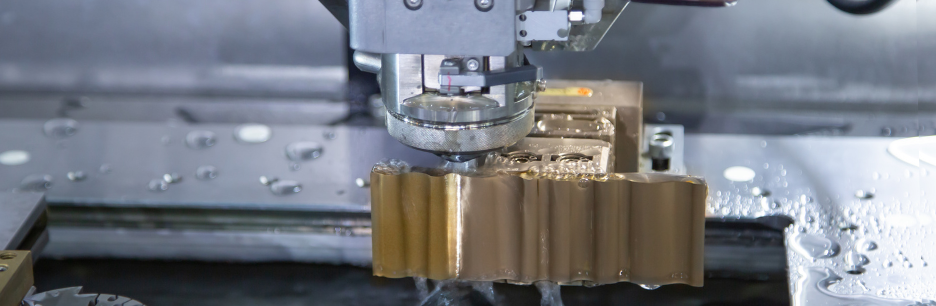
The Importance of Water Chillers in EDM Applications
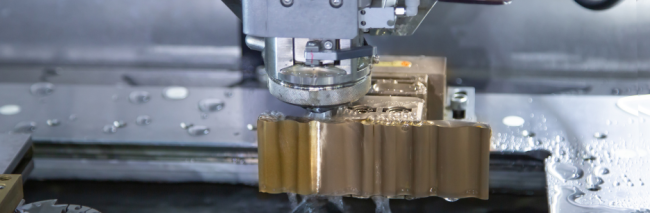
Electrical Discharge Machining is a sophisticated manufacturing process that has revolutionized the way businesses create complex, precise components. This non-traditional machining method has gained popularity in industries such as aerospace, automotive, and medical device manufacturing due to its ability to process hard materials and create intricate shapes with exceptional accuracy.
And at the heart of EDM’s success lies the critical role of water chiller systems in maintaining optimal temperature control throughout the machining process.
What is Electrical Discharge Machining?
Electrical Discharge Machining is a unique technique that harnesses electrical sparks’ power to remove material from a workpiece.
How it Works
The process begins by submerging the workpiece in a dielectric fluid, which is usually deionized water or oil. A shaped electrode, often made of graphite or copper, is positioned close to the workpiece. By applying a high-frequency current between the electrode and the workpiece, a series of controlled electrical sparks can be generated. These sparks cause the workpiece material to melt and vaporize, eroding it to create the desired shape or contour.
Advantages
One of the benefits of EDM is its ability to machine materials that are notoriously difficult to process using traditional machining methods. These include hard metals, alloys, and even conductive ceramics. Its non-contact nature eliminates the need for cutting forces, allowing it to create delicate and intricate features without inducing mechanical stress on the workpiece.
The Role of Water Chillers in Optimizing EDM Processes
While EDM offers many benefits, it also presents a unique challenge in terms of temperature control. The electrical sparks generated during the process can cause the dielectric fluid to heat up rapidly. If left unchecked, this temperature rise can cause issues that compromise the efficiency and quality of the EDM operation.
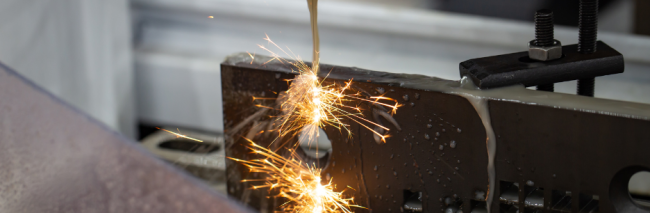
Firstly, elevated temperatures can cause the dielectric fluid to break down, diminishing its insulating properties. This can result in unstable and inconsistent machining, as the electrical sparks become erratic and less controlled. Secondly, the heat generated by the sparks can cause distortion and expansion of the workpiece and electrode, leading to inaccuracies and poor surface finishes. Lastly, excess heat can accelerate the wear and tear of the electrode, reducing its lifespan and increasing the frequency of replacements.
Water chillers remove heat generated during EDM and dissipate it from the machining zone, ensuring a stable and consistent thermal environment. The working principle of an industrial process chiller is relatively straightforward. Firstly, dielectric fluid is pumped from the EDM machine’s tank into the chiller unit. Inside the chiller, the fluid passes through a heat exchanger, where a refrigeration system cools it. The chilled fluid is then returned to the EDM tank, where it can effectively absorb the heat generated by the electrical sparks. This continuous circulation and cooling cycle maintains the dielectric fluid at the right temperature, typically between 68°F and 77°F.
Benefits of Using Water Chillers in EDM Processes
Consistent Cooling
One of the main advantages of using water chillers in EDM is maintaining a stable and consistent temperature throughout the machining process. By precisely controlling the temperature of the dielectric fluid, water chillers eliminate the fluctuations and variations that can occur due to the heat generated by electrical sparks. This consistency in cooling is vital for achieving uniform machining results, as it minimizes thermal distortion and ensures the workpiece and electrode maintain their desired dimensions.
Improved Machining Performance
Using water chillers in EDM processes directly impacts the overall machining performance. By keeping the dielectric fluid at a stable and optimal temperature, water chillers enable faster machining speeds and higher material removal rates. This is because consistent cooling prevents the formation of gas bubbles and reduces the occurrence of short circuits, allowing for more efficient and uninterrupted machining.
Reduced Thermal Stress
EDM processes generate high temperatures due to the energy of the electrical sparks. Without proper industrial cooling, these elevated temperatures can induce thermal stress on the workpiece and the electrode. Thermal stress can manifest in various ways, such as deformation, warping, cracking, or even complete failure of the machined components.
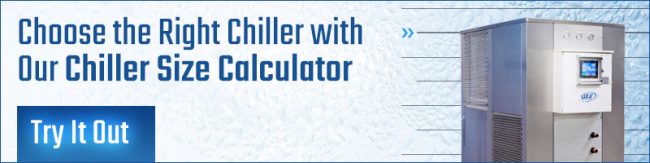
Discover Cold Shot Chillers’ Machining Equipment Cooling Solutions
Cold Shot Chillers recognizes the role that industrial chillers play in optimizing EDM processes and ensuring consistent, high-quality machining results. With our extensive expertise and commitment to innovation, we offer a comprehensive range of machining equipment cooling solutions designed to meet EDM applications’ demanding requirements.
Our process chillers for EDM machines feature advanced temperature control systems, robust construction, and user-friendly interfaces. These chillers deliver precise and reliable cooling performance, ensuring the dielectric fluid is maintained at the optimal temperature range throughout the machining process.
To learn more about our cutting-edge water chillers for EDM applications and how they can benefit your manufacturing operations, please reach out to our team.