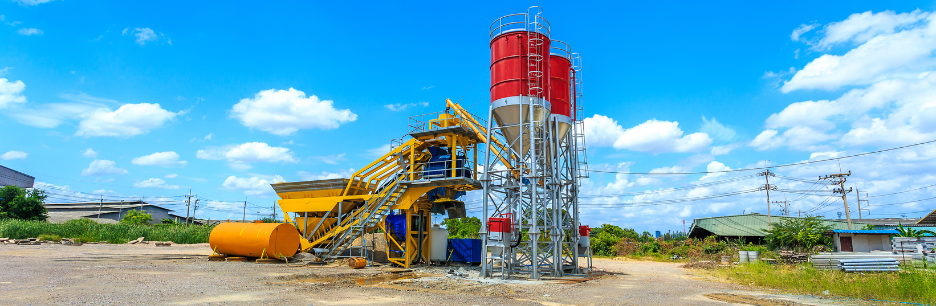
Water Chillers for Concrete Cooling Plants: What You Need to Know
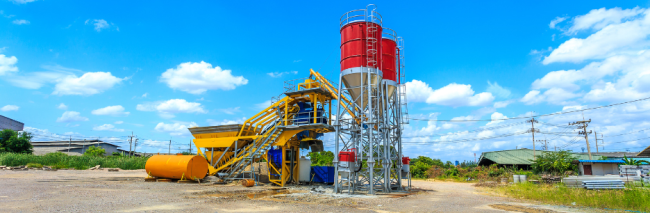
Concrete production demands precise temperature control to ensure quality and workability, especially in warm climates or during peak summer months. When concrete overheats during the mixing process, it can lead to issues with setting time and reduce the overall strength of the finished product. Industrial water chillers for concrete cooling plants offer a practical and efficient solution to these challenges by providing reliable cooling directly to the mix.
The Role of Temperature Control in Concrete Production
Temperature control is critical for achieving uniform quality and durability across concrete production batches. During mixing, the exothermic reactions between cement and water generate significant heat, which can raise the concrete’s temperature. Elevated temperatures accelerate hydration rates, potentially leading to a faster setting time and increased risk of cracking or compromised strength.
For large-scale projects with high production volumes, consistent temperature regulation is vital to maintain optimal curing rates and prevent early setting. Water-cooled chillers serve as effective cooling systems, precisely managing the temperature of mixing water and aggregate to keep concrete within ideal thermal ranges for peak strength and workability.
How Water Chillers Operate in Concrete Cooling Plants
Water chillers in concrete cooling plants function by reducing the temperature of the water used in the concrete mix, a key step in managing thermal conditions during production. By circulating chilled water directly into the mixing drum or plant, these systems help offset the heat generated during the mixing process, ensuring consistent and controlled batch temperatures. This precision is crucial for maintaining the structural integrity and durability of the final product.
Cold Shot Chillers provides advanced industrial water chillers specifically engineered for concrete plants. These systems are designed to handle high-production environments, delivering continuous cooling for large volumes of water to meet the demands of intensive concrete manufacturing processes.
Benefits of Using Water Chillers in Concrete Cooling
Integrating water chillers into industrial cooling plants offers several technical advantages that enhance production quality and efficiency.
Improved Concrete Strength and Durability
Maintaining lower concrete temperatures during production improves hydration control, leading to stronger molecular bonds within the cement paste. This reduces the likelihood of thermal cracking, ensuring a more durable final product, particularly in large-scale applications requiring structural integrity.
Temperature Uniformity for Consistent Batches
Water chillers provide precise control over batch temperatures, maintaining consistent thermal conditions across all production cycles. This uniformity is vital for meeting stringent engineering specifications, ensuring homogeneity in material properties, and reducing the potential for rework or waste.
Cost-Effective Cooling Solutions
Compared to methods like ice dosing or liquid nitrogen injection, water chillers offer a more energy-efficient and sustainable cooling process. These systems reduce operational costs over time while delivering the large-scale cooling capacity necessary for industrial concrete batch plants.
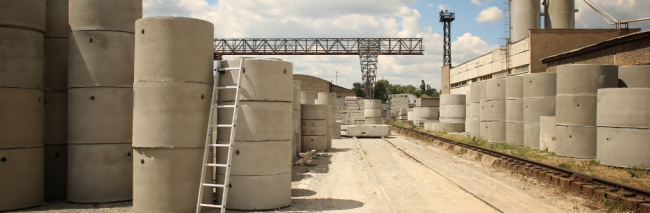
3 Things to Consider When Choosing a Chiller for Your Concrete Plant
Selecting the ideal water chiller for your concrete cooling plant involves balancing capacity, efficiency, and durability to meet the specific demands of your operations. Here’s what to keep in mind:
- Chiller Cooling Capacity – The chiller must have the appropriate cooling capacity to handle the water volume required for your plant’s production output. This includes accounting for the ambient temperature, the desired water temperature, and the mixing cycle’s thermal load. Undersized systems may lead to inconsistent cooling, impacting the quality of the concrete.
- Chiller Energy Efficiency – Energy consumption is a significant factor in long-term operational costs. High-efficiency chillers, often rated by their coefficient of performance (COP), provide effective cooling while minimizing energy usage. Investing in energy-efficient models can reduce utility expenses and support sustainable operations.
- Chiller Reliability & Durability – For demanding applications like concrete production, industrial-grade chillers are crucial to avoid costly downtime. Choose systems built for continuous operation, with corrosion-resistant components and advanced controls for reliable performance.
What Size Water Chiller Do You Need?
The right size water chiller for your concrete batch plant depends on your production volume and cooling requirements. Accurate calculations ensure consistent concrete temperatures and optimal performance. Cold Shot Chillers can help you select the perfect system for your needs.
Concrete Batch Plant Chiller Sizing >
Cold Shot Chillers: Your Partner in Concrete Cooling
At Cold Shot Chillers, we understand the specific cooling needs of concrete production. Our water chillers for concrete cooling plants are engineered to offer efficient, consistent, and reliable cooling solutions tailored to high-volume demands. If your team is setting up a new plant or upgrading an existing cooling system, Cold Shot Chillers is ready to help you find the right chiller to keep your concrete at optimal temperature.
Get in touch with us today to learn more about our solutions for concrete cooling and how we can support your next project with industrial-grade chillers that are built to last.