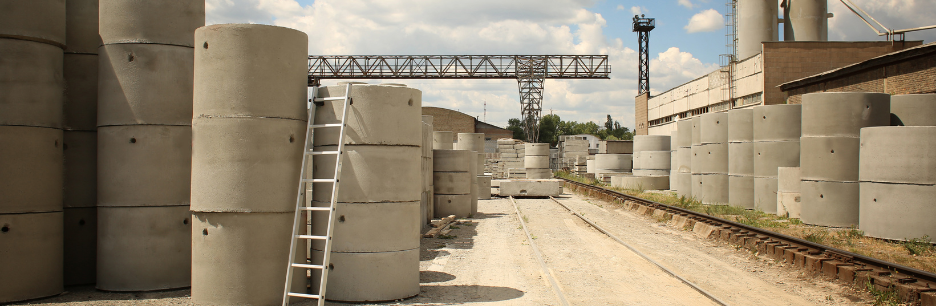
What Size Water Chiller Do You Need for a Concrete Batch Plant?
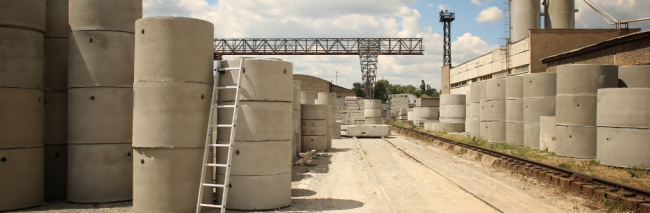
Concrete batch plants often face challenges related to temperature variations, which can lead to inconsistent results. Fluctuations in temperature may cause issues such as uneven curing, delayed setting times, and compromised concrete strength. Therefore, adequate temperature control through water chillers is critical to concrete batch plant operations.
The Importance of Temperature Control in Concrete Production
Consistent and precise temperature regulation is vital for producing high-quality concrete. Cooling systems help maintain the correct temperature of the mixing water, influencing factors such as setting time and workability. This not only enhances the overall quality of the concrete but also contributes to the efficiency of the batching process.
By mitigating temperature-related challenges, industrial cooling systems enable concrete producers to achieve reliable and standardized results.
What is a Batching Plant Chiller?
A batching plant chiller is a specialized cooling unit designed to regulate and control the temperature of water used in the concrete batching process. The chiller is integrated into the concrete batch plant’s system and operates in coordination with the mixing process.
How it Works
- Temperature control – The chiller contains a refrigeration system that cools a heat exchange unit, often a coil or plate, through which the mixing water flows.
- Cooling the water – As the mixing water passes through the heat exchange unit, it absorbs the cold from the refrigerant, effectively lowering its temperature.
- Integration with the batching process – The chilled water is then introduced into the concrete mix during the batching process. This controlled temperature helps offset the heat generated during mixing, preventing issues associated with elevated temperatures.
- Optimizing concrete properties – By maintaining the desired temperature of the mixing water, the chiller ensures optimal concrete properties, such as setting time, strength development, and workability.
- Continuous operation – The chiller operates continuously to provide a consistent and controlled temperature environment for the mixing water, contributing to the overall quality and performance of the concrete produced.
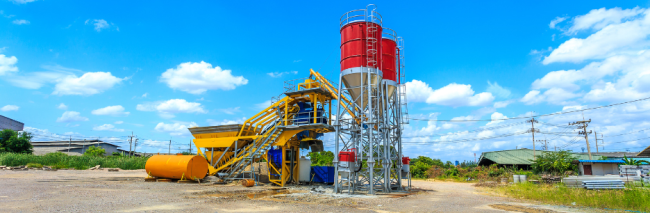
Concrete Batch Plant Chiller Sizing
Water-cooled chillers for concrete batching plants typically range from 30-400 tons.
The size of the water chiller needed for a concrete batch plant depends on several factors, including the production capacity of the plant, the ambient temperature of the location, and the desired temperature of the mixing water. Generally, the water chiller should have sufficient cooling capacity to offset the heat generated during the concrete mixing process.
A smaller water chiller may suffice for smaller concrete batch plants with lower production capacities, while larger plants with higher production rates may require more powerful chillers. It’s essential to consider the specific requirements of the plant and consult with experts in the field to determine the appropriate size of the water chiller.
Factors such as the local climate and the need for precise temperature control will also influence the selection of an adequately sized water chiller for optimal concrete production.
Installation Tips for Batching Plant Chillers
Installing industrial chillers in concrete batch plants requires careful planning and adherence to specific guidelines to ensure optimal performance and safety. Here are some general guidelines:
- Conduct a thorough site assessment to determine the most suitable location for the water chillers. Consider factors such as accessibility, proximity to the batching plant, and environmental conditions.
- Ensure there is sufficient space to install the water chillers and associated equipment. Consider factors such as clearance for airflow, maintenance access, and future expansion needs.
- Verify the electrical infrastructure at the chosen location meets the power requirements of the water chillers. Coordinate with electrical contractors to ensure proper wiring and connections.
- Ensure a reliable and adequate water supply for the chillers. Install proper filtration systems to prevent debris and impurities from affecting the chiller’s performance.
- Provide a stable foundation or mounting structure for the water chillers. This foundation should be able to support the weight of the chillers and minimize vibrations.
- Ensure proper ventilation around the chillers to dissipate heat effectively. Adequate airflow is essential for the refrigeration system’s efficiency and overall chiller performance.
- Implement safety measures, such as installing safety guards and warning signs, to prevent accidents and ensure the well-being of personnel working near the water chillers.
- Verify that the installation complies with local building codes, safety regulations, and environmental standards. Obtain any necessary permits before initiating the installation.
Learn More About Cold Shot’s Concrete Batch Mixing Chillers
Step up your concrete production with Cold Shot Chillers. Browse now to access reliable and efficient solutions designed to optimize water temperatures during the mixing process. Our water chillers are your key to achieving consistent and high-quality concrete results, ensuring the success of your batching operations.
Contact a specialist now for more information about our commercial chiller systems and other cooling solutions.