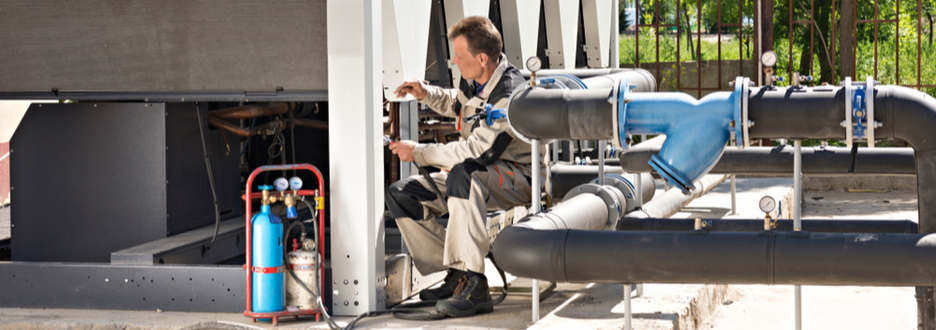
CHILLER SAFETY – SAFETY SWITCHES AND CUT-OUTS
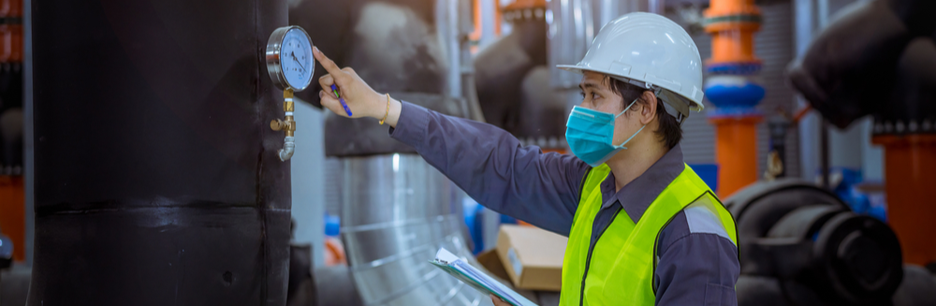
Industrial chillers play a vital role in maintaining process temperatures across several industries. Brewery glycol chillers, MRI chillers, and hydroponic water chillers are just a few examples of this equipment being used in different trades.
While the benefits of using a process chiller for heat-sensitive applications are well-established, operators must ensure these cooling systems are used according to the manufacturer’s instructions. Owners and users must familiarize themselves with all the safety features of their chiller units to ensure smooth operating with minimal potential hazards.
Why Is Chiller Plant Safety Important?
Like every other type of industrial equipment, chillers require operators to take necessary safety precautions. Ignorance of the potential hazards that chillers can pose may lead to industrial accidents such as refrigerant leakages or explosions that could cause bodily harm to workers.
To prevent these accidents, all chiller units must be operated within certain safety parameters.
Dangers of a Lack of Chiller Safety
Industrial chillers use refrigerants that circulate in closed channels to achieve cooling. Maintaining the integrity of these refrigerant systems requires strict adherence to laid down safety and maintenance protocols.
Some types of chiller refrigerant can pose a serious environmental hazard to surrounding workers if they don’t have adequate knowledge of chiller safety features that cut off refrigerant circulation in case of a leak.
Common Chiller Safety Switches and Features
Typical chiller units come preinstalled with various switches and features that help prevent the onset of industrial hazards during their operation. Operators must familiarize themselves with all these features to ensure an efficient and safe process.
Outlined below are some key safety features that standard industrial chiller units possess.
Flow Safety Thermostat
A vital safety feature in industrial chillers is the flow safety thermostat. These devices detect adverse changes in temperature within the refrigerant circuit. When unfavorable thermal conditions arise within the chiller’s refrigeration unit, the flow safety sensor will detect it and cut off the coolant circulation. Although different circumstances can trigger the safety flow thermostat, the most common cause is a clogged strainer.
A tripped flow safety thermal sensor will require manual resetting by a technician; however, operators must accurately determine the triggering cause to prevent further damage to the process cooling system.
Freeze Safety
Industrial chillers also come equipped with low-temperature sensors. Freeze safety devices detect low thermal levels and switch off to prevent the refrigerant from freezing over. An automatic reset occurs when the temperature of the chiller fluid returns to normal levels.
Liquid Flow Switch
Another safety feature of a typical chiller system is the liquid flow switch. This mechanism detects a reduction in the volume of fluid entering the evaporator and automatically cuts off flow. The switch resets when fluid levels are restored to normal.
Compressor Safety Features
Compressor units are a key part of refrigeration systems including those in chiller units. These compressor devices handle refrigerants circulating under a tightly regulated pressure range. Sudden increases or decreases in the pressure levels within a compressor unit can cause significant damage to the cooling unit and expose operators to toxic chemical leakages.
To ensure compressor pressure is kept within safe limits, most units are manufactured with three safety features:
- High pressure cut out
- Low pressure cut out
- Low oil pressure cut out
Compressor Low-Pressure Safety
Low pressure cut out devices help protect the chiller unit compressors against an adversely low pressure while preventing the entry of air into the system in cases where a vacuum develops. Further, low-pressure safety units shut down refrigerated compartments when there is an obstruction to gas return with a corresponding reduction in system pressure. Low-pressure safety switches automatically restore chiller function once compressor pressures have normalized.
Compressor High-Pressure Safety
Elevated pressure levels within a chiller compressor unit can be attributed to various causes including cooling water loss, high environmental temperatures, and gas discharge line obstruction. To protect the compressor from the damaging effects of high pressures, a cut off automatically detects and shuts it down.
By design, high-pressure cut-offs must be manually reset. This ensures operators investigate the possible causes of the compressor shut down before restarting the system.
Compressor Low Oil Pressure Safety
The oil used to prevent friction within the bearings of a compressor is usually under pressure by an attached oil pump. A faulty pumping mechanism will reduce the amount of oil reaching the bearings thus exposing them to rapid wear. The use of a compressor low oil safety cut out will switch off the compressor once it detects a fall in the pressure of the lubricant oil supplied to it.
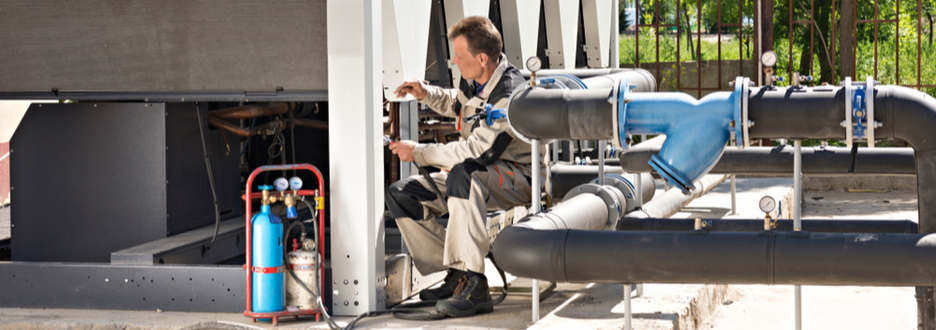
Trust Cold Shot Chillers for Dependable Industrial Chiller Units
For more than thirty years, Cold Shot has been among the leading industrial chiller manufacturers in the US. As we continue to manufacture the best industrial cooling solutions, the provision of a world-class satisfactory customer experience remains our top priority.
Request a quote on one of our units today, or find more information about the wide range of air-cooled chillers and water-cooled chillers that we offer on our website.
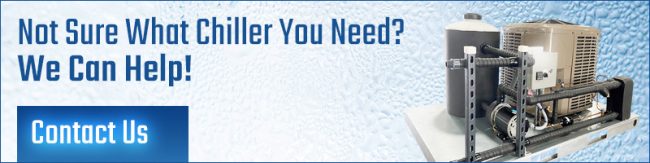