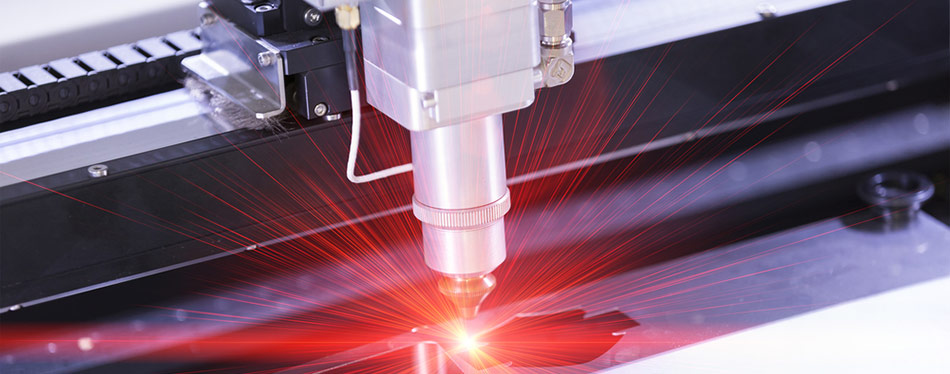
How Chillers Enhance the Performance of Industrial Lasers
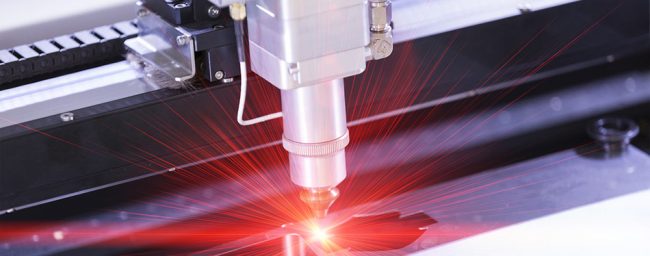
Industrial lasers are high-powered devices used in various manufacturing processes to cut, weld, engrave, and perform other precision tasks. They emit concentrated beams of light that generate significant amounts of heat during operation. Maintaining stable operating temperatures is essential for achieving precise laser beam characteristics and ensuring consistent results.
What is an Industrial Laser Chiller?
An industrial laser chiller is a specialized cooling system designed to maintain precise temperature control for laser equipment. These chillers are essential in laser applications where consistent operating temperatures are critical for maintaining beam quality, precision, and equipment longevity.
These industrial chillers typically feature robust cooling capacity, advanced temperature control mechanisms, and specific safety features to ensure optimal performance of laser systems in various manufacturing and industrial processes.
How Do They Work?
Laser chillers work by circulating a coolant, typically water or a water-based fluid, through the laser system to remove excess heat generated during operation. Here’s a simplified explanation of how they work:
- Coolant Circulation: The chiller circulates coolant through a closed-loop system that includes the laser resonator and other critical components such as optics and beam delivery systems.
- Heat Absorption: As the coolant flows through the laser components, it absorbs heat generated by the laser’s operation. This heat is transferred from the laser components to the coolant.
- Heat Dissipation: The heated coolant is then pumped out of the laser system and into the chiller unit.
- Cooling Process: Inside the chiller unit, the coolant passes through a heat exchanger where the heat is transferred to another medium, such as air or a separate water circuit, depending on the chiller’s design.
- Temperature Regulation: The chiller’s control system monitors the temperature of the coolant and adjusts the cooling capacity as needed to maintain a consistent and optimal operating temperature for the laser system.
- Heat Rejection: Finally, the cooled coolant is returned to the laser system to continue the cooling cycle, effectively managing the temperature of the laser components and ensuring stable performance.
Laser coolers may also incorporate additional features like filtration systems to maintain coolant purity, advanced control interfaces for monitoring and adjusting temperature settings, and safety mechanisms to protect against overheating or coolant failure.
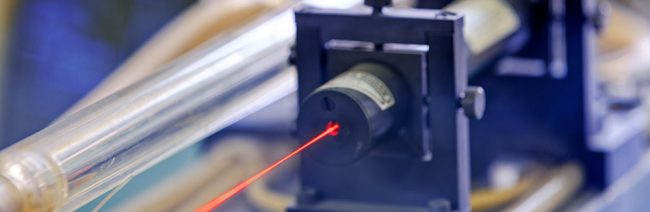
Why You Should Be Using Chillers for Your Industrial Lasers
Enhanced Beam Quality & Consistency
Stable temperatures provided by chillers help maintain consistent beam quality, ensuring sharp focus and minimal divergence. This consistency is crucial for applications requiring high precision and repeatability, such as microelectronics and medical device manufacturing.
Extended Laser Lifespan
By preventing overheating and thermal stress, chiller units extend the lifespan of industrial lasers. They reduce wear on sensitive components, such as laser diodes and mirrors, minimizing downtime and maintenance costs over time.
Improved Efficiency & Productivity
Reliable temperature control from chillers enhances operational efficiency by reducing downtime for recalibration or cooling-off periods. This increased productivity translates into higher throughput and lower production costs for manufacturers.
What Types of Lasers Require Cooling?
Most types of lasers used in industrial, medical, and scientific applications require cooling to manage heat dissipation, maintain stable operating temperatures, ensure precise beam quality, and extend equipment lifespan.
- CO2 Lasers: Commonly used in cutting, engraving, and welding applications, CO2 lasers operate at high power levels and generate significant heat. They require cooling to maintain stable beam quality and prevent overheating of optics and resonators.
- Solid-State Lasers: Solid-state lasers, such as Nd and fiber lasers, are used in materials processing, marking, and medical applications. They also generate heat during operation and require cooling to ensure precise beam control and efficiency.
- Diode Lasers: Diode lasers are used in diverse applications, including telecommunications, medical treatments, and materials processing. While they are generally more compact than other types, diode lasers still require cooling to manage heat dissipation and maintain reliability.
- Excimer Lasers: Used in semiconductor manufacturing, photolithography, and medical applications, excimer lasers produce short-wavelength ultraviolet light. They operate at high energy levels and require efficient cooling to prevent overheating and ensure stable performance.
- Dye Lasers: These lasers use organic dye solutions as the lasing medium and are used in spectroscopy, scientific research, and medical diagnostics. Dye lasers require cooling to stabilize the dye solution temperature and maintain optical performance.
Choosing the Right Chiller for Your Laser System
Selecting the appropriate industrial chiller depends on factors like laser power, cooling capacity requirements, and environmental conditions. Cold Shot Chillers offers a range of customizable solutions designed to meet the specific needs of industrial laser applications. Our expert team can help you choose the right chiller to maximize the performance and longevity of your laser system.
Improve Your Laser Performance with Cold Shot Chillers
Did you know that our industrial chiller manufacturers offer precision cooling solutions designed to optimize the efficiency, reliability, and longevity of your laser systems? So, whether you’re in metal fabrication, electronics manufacturing, or medical device production, our custom chiller systems ensure stable temperatures for consistent beam quality and operational excellence.
Contact our team to discuss your cooling requirements and discover what Cold Shot Chillers can do to help.
