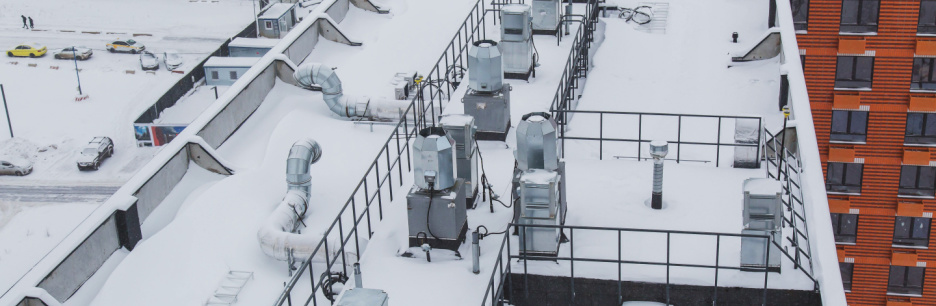
HOW TO MAINTAIN CHILLERS IN WINTER WEATHER CONDITIONS
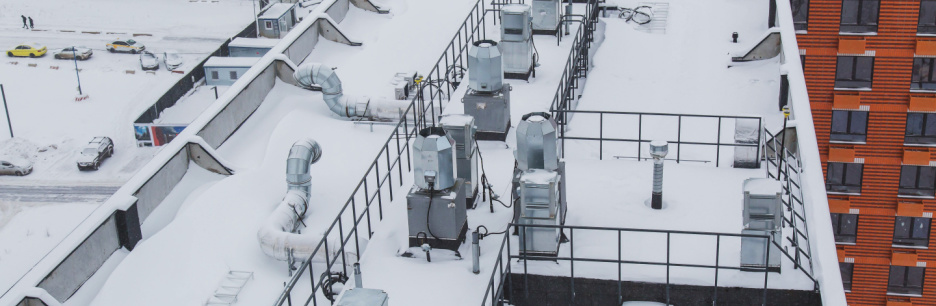
Unlike the wrong perception that industrial chillers are expendable during cold seasons, such as winter, these units are vital to industrial applications all year round. Neglecting chillers during this period makes them susceptible to damage and a high maintenance cost. Thus, industrial operators must implement good maintenance practices in winter weather conditions. This article highlights some of these practices and tips for ensuring high-efficiency chiller operations regardless of the weather conditions.
Industrial Chillers and Cold Weather: An Overview
Cold winter temperatures can be harmful to chiller units. Moreover, the weather can lead to power outages, which can significantly minimize the efficiency of the units. Operators must acknowledge that many types of chillers may hold onto their initial temperature levels within a limited timeframe during power outages.
Thus, industrial chiller applications may suffer setbacks and downtime. Operators must put effective coping strategies in place to prepare for such uncertainties. Moreover, the operators must consider the age of the chiller since the older ones can develop issues, such as fissures and breaches, which can significantly worsen during colder temperatures and cause irreparable equipment damage.
Other winter-related chiller concerns include the high susceptibility of the heat transfer fluid to freezing, fan blade damage due to snow or ice, and head pressure drop. Therefore, operators must consistently monitor the glycol charts, restrict airflow through the chiller condenser, and use manual head pressure controls to address these potential issues adequately.
Additionally, cracks and leakages, improper electrical connections, and faulty pump, safety, piping, and control systems can significantly impede the proper functioning of industrial chillers during cold weather conditions.
Tips for Winter Chiller Operation
Some common tips for operating industrial chiller units during the winter season include:
- Ensuring a proper mixture of glycol within the unit
- Cleaning and clearing snow and ice from the chiller condenser
- Properly controlling head pressures
- Ensuring sufficient supply of heat to avoid refrigerant or glycol freezing
- Planning ahead for chiller repairs
Glycol is vital for industrial chillers due to its anti-freezing capabilities. However, chillers require a proper mixture of this element to achieve high-efficiency anti-freezing operation. Thus, operators must leverage glycol charts to identify the prevalent ambient temperature and the glycol levels ideal for the chiller’s proper functioning.
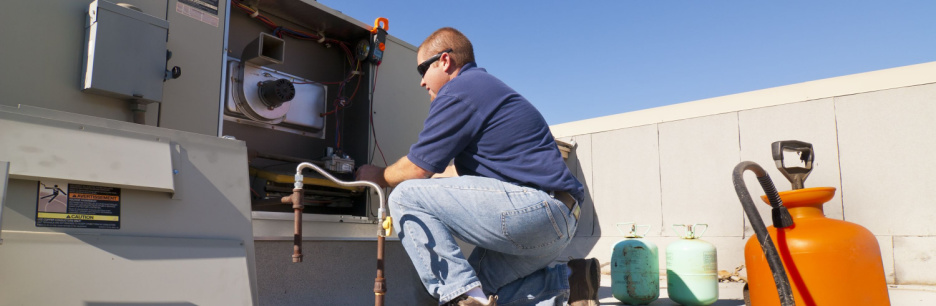
Moreover, operators must constantly monitor the glycol levels using a refractometer and use adequate glycol types, such as inhibited propylene glycol, which is ideal for heat ventilation and air conditioning (HVAC) systems. Similarly, since ice and snow are detrimental to chiller fan blades and can impede condenser airflow, operators must constantly monitor the condenser for these elements and regularly remove them through the winter season.
Cold temperatures in the season can also lead to head pressure drops, especially for chiller units that lack ambient controls, such as flooded condensers and fan cycling. This issue can affect the chiller operation. Thus, in addition to manually controlling the head pressure, a simple technique of wrapping the condenser with plastic or blocking the condenser intake with a cardboard fix can address the issue. Finally, while allowing the chiller pump to run constantly, even during non-peak periods, can generate sufficient heat to prevent refrigerant and glycol freezing, planning can significantly address several common chiller problems.
Winter Chiller Maintenance Best Practices
Operators can opt for renting a chiller unit during winter, especially if the existing one is inefficient in light of prevalent conditions. However, this option is highly cost-intensive and may be economically inviable. Thus, incorporating acceptable chiller maintenance practices into existing operations can ensure proper functioning all year round. Some of these practices include:
- Constant cleaning of the chiller
- Inspecting the chiller for leakages
- Ensuring proper evaporation
- Inspecting chiller piping insulation
- Monitoring and analyzing oil and chiller refrigerant levels
Cleaning chillers to eliminate deposits can significantly minimize energy consumption by up to 30%. Cleaning is a vital chiller safety practice because deposits can cause temperature increases, escalating the compressor burden to compress the refrigerant and block airflow.
Daily inspection of winter chillers for leakages is essential to maximizing the equipment’s performance and ensuring improved system operation. While proper evaporation allows winter chillers to handle water temperature and pressure changes, inspecting the chiller piping insulation can eliminate mold formation and spread across the unit. Finally, monitoring and analyzing oil and refrigerant levels are crucial for identifying leakages and prevalent contaminants, such as acids, moisture, and metals.
Make chiller preventive maintenance easy with the Cold Shot Guardian™ App.
Cold Shot Manufactures Reliable Winter Chillers
Cold Shot Chillers is dedicated to manufacturing and installing high-quality industrial chillers that meet global industry standards. We offer various cost-effective and reliable chillers that are ideal for all temperature ranges, including extreme temperatures in winter.
Kindly consult us today to make a confident decision about buying your next winter chiller.