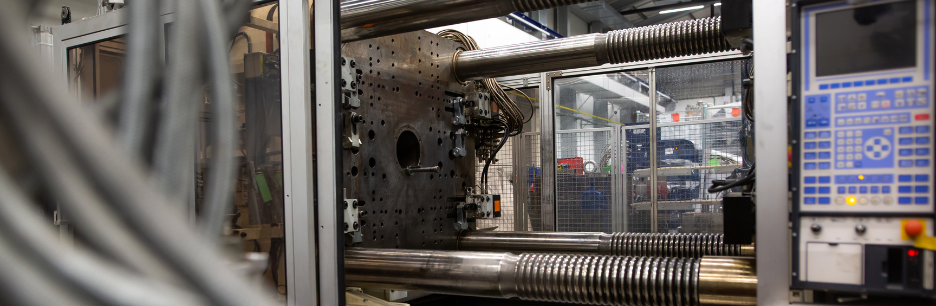
Optimizing Injection Molding Processes: The Role of Chillers
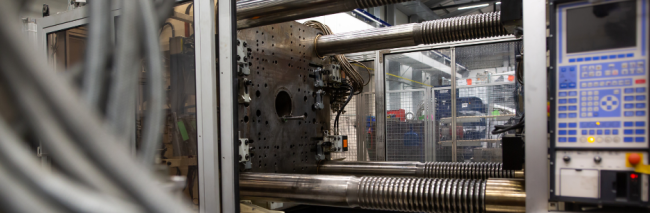
If you’re in the world of injection molding, you know how crucial it is to maintain precise temperatures throughout the process — and a key player in this equation is industrial chillers. Keep reading to learn why chillers are essential and how they enhance efficiency and quality in injection molding operations.
Why Chillers Matter in Injection Molding
Injection molding involves melting plastic pellets and injecting them into molds to produce a wide range of products. Maintaining consistent temperatures during this process is critical to achieving high-quality parts and preventing defects like warping or shrinkage.
Process chillers play a pivotal role in cooling the molds and ensuring that the plastic solidifies correctly before being ejected.
Injection Molding Process
The injection molding process consists of several key steps, each crucial to producing high-quality plastic parts.
- Injection: The first step involves injecting molten plastic material into a mold cavity under high pressure. Once the mold is filled, the injection phase concludes, and the cooling stage begins.
- Cooling: Cooling is perhaps the most critical phase in injection molding. Proper cooling ensures that the plastic solidifies uniformly, minimizing internal stresses and preventing defects like warping or shrinkage. Chillers are essential during this phase as they provide the necessary cooling to rapidly and consistently lower the mold temperature to the desired level. The system’s precise temperature control capabilities ensure optimal cooling rates, resulting in faster cycle times and improved part quality.
- Ejection: Once the plastic has solidified and cooled sufficiently, the mold opens, and the ejector mechanism pushes the finished part out of the mold cavity. Proper cooling facilitated by injection molding chillers ensures that the part retains its shape and dimensions, allowing for smooth ejection without damage or deformation.
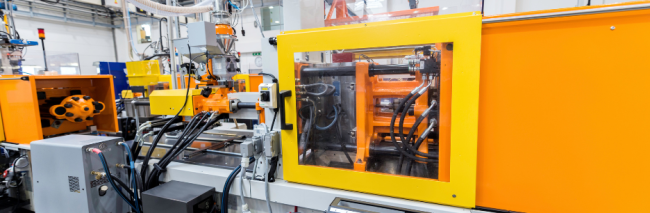
How Chillers Enhance Efficiency
Industrial chillers are designed to provide precise and reliable cooling control, allowing for consistent temperatures throughout the injection molding cycle. Investing in the right water chiller unit brings several advantages that directly contribute to operational success and product quality:
- Consistent Cooling: A chiller system maintains precise temperatures, ensuring consistent cooling of molds. This consistency minimizes variations in part dimensions and reduces the likelihood of defects like warping or sink marks.
- Faster Cycle Times: Optimal cooling facilitated by a chiller system can lead to shorter cycle times. Quicker cycles translate to increased production throughput and overall efficiency.
- Improved Part Quality: Proper cooling provided by injection molding chillers results in improved part quality. Enhanced dimensional stability and reduced internal stresses lead to higher-quality finished products.
- Energy Efficiency: Modern water chiller systems are designed for energy efficiency, helping to lower operational costs by reducing energy consumption without compromising performance.
- Minimized Material Waste: By preventing defects such as warping and shrinkage, chillers reduce material waste. This not only saves on material costs but also supports sustainable manufacturing practices.
- Extended Tool Life: Consistent cooling and controlled temperatures extend the lifespan of injection molds, reducing the need for frequent mold replacements and maintenance.
- Process Control: Chillers offer precise temperature control, enabling operators to fine-tune cooling parameters for different materials and molds. This level of control enhances process repeatability and product consistency.
- Reduced Downtime: Reliable cooling provided by chillers helps minimize downtime due to mold-related issues, leading to increased production uptime and overall equipment effectiveness (OEE).
Incorporating a chiller system into your injection molding setup is a strategic investment that yields tangible benefits in terms of operational efficiency, product quality, and cost savings.
Cold Shot Chillers’ tailored chiller solutions maximize these benefits, empowering your injection molding processes to achieve optimal performance and success.
Explore Our Injection Molding Chillers
When selecting an injection molding chiller, factors such as cooling capacity, temperature control accuracy, energy efficiency, and footprint are crucial considerations. Our team of experts is here to guide you through the selection process, recommending the best chiller solution based on your specific requirements and budget.
Ready to optimize your injection molding processes with reliable cooling solutions? Explore our range of plastic processing chillers and discover how Cold Shot Chillers can help you achieve greater efficiency and consistency in your operations.
Contact us today for personalized assistance, and let’s take your injection molding processes to the next level!