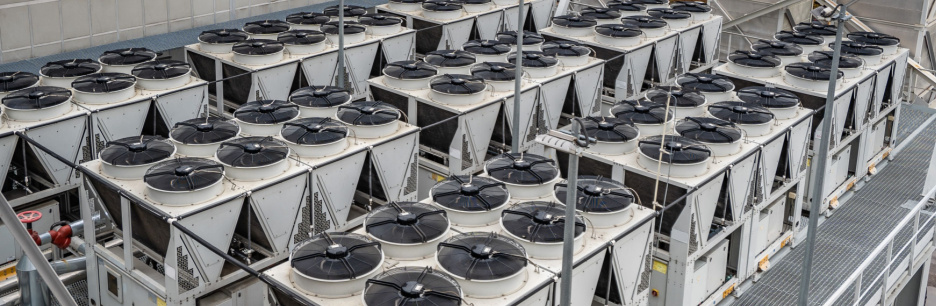
How to Use Your Chiller More Efficiently in 2025 + Chiller Efficiency Formula
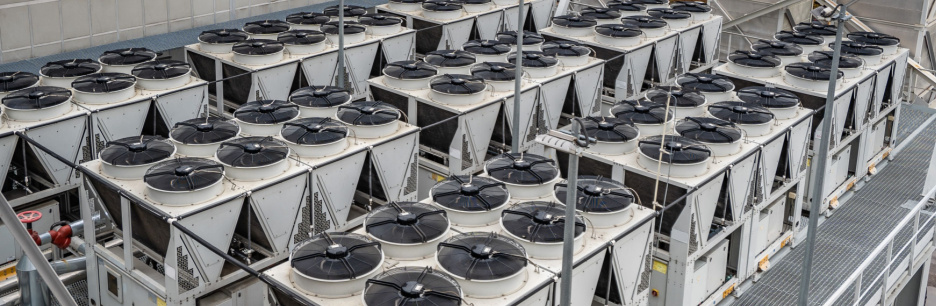
Many manufacturing and processing companies rely on industrial chillers to provide cooling for everything from machinery to finished goods. However, these systems use a lot of electricity, accounting for a large portion of energy use. Finding ways to make chillers run more efficiently is more important than ever. Here are some tips for increasing water and air-cooled chiller efficiency in 2025.
Why Optimal Chiller Efficiency Matters for Your Operations
Improving chiller efficiency can save money on electricity and reduce energy waste, which in turn helps lower carbon emissions.
Therefore, reducing the energy consumption of your industrial chiller benefits the environment by lowering greenhouse gas emissions and other pollutants. In addition, companies that can effectively use industrial chillers can gain a competitive advantage by reducing their production costs. This can ultimately help them become more profitable and sustainable in the long run.
How to Calculate Chiller Efficiency
Calculating chiller efficiency is easy when you use a formula based on the “coefficient of performance” (COP). COP measures the ratio of the cooling provided by the chiller (refrigeration effect) to the electrical energy it consumes. Both values are expressed in kilowatts (kW). This ratio helps determine how effectively the chiller uses energy.
For example, if an industrial chiller produces 3,000 kW of cooling while consuming 500 kW of electrical energy, its COP will be:
3,000 kW / 500 kW = 6
This means that the chiller produces 6 kW of cooling for every 1 kW of electricity consumed.
For the imperial calculation, you first have to convert BTU to kW. If your chiller’s total cooling is measured in BTU, multiply it by 0.000293 to convert it to kW before using this chiller efficiency formula.
6 Ways to Maximize Chiller Efficiency
The following tips can help maximize the efficiency of your industrial chiller:
1. Conduct Routine Maintenance
Keep a record of the system’s condition so you can easily detect any common chiller problems with the system. This will allow you to perform regular chiller maintenance to ensure that the unit operates at peak efficiency and reduces the likelihood of a breakdown.
A few examples of important maintenance include:
- Inspect and clean condenser coils regularly
- Check refrigerant levels and refill if needed
- Monitor and replace air or water filters
- Verify pump operation and inspect for leaks
- Test electrical connections and control panels
It is preferable to have a qualified technician perform the chiller repairs and preventative maintenance, particularly for tasks requiring technical knowledge, such as refrigerant handling.
2. Maintain Proper Refrigerant Levels
We mentioned refrigerant checks in routine maintenance — now let’s break down why keeping proper refrigerant levels is so important.
The efficiency of a chiller is closely related to how well the compressor can pump the refrigerant through the system. As a result, maintaining proper chiller refrigerant levels is critical to ensuring the compressor’s efficiency. Leaks are the primary cause of low refrigerant levels. So, make sure to monitor changes in refrigerant levels so that you can detect leaks.
3. Have An Effective Water Treatment Program
Open cooling sources in chiller condenser water loops can cause fouling and damage to the tubes, piping, and other materials. These may pit the tubes and decrease their effectiveness.
A cooling tower blowdown, for example, can assist in the removal of solids and contaminants. You can also carry out a visual inspection to ensure general water quality.
Expert Tip: Schedule a quarterly cleaning of cooling tower basins to remove debris and sludge that can harbor biological growth, improving overall system efficiency.
4. Don’t Neglect Fluid Quality
Chiller units have condenser and evaporator coils that require proper cleaning and monitoring. Impurities, scale, or debris can build up on condenser and evaporator coils, reducing heat transfer and forcing the system to work harder.
You should regularly test and treat the fluid to prevent corrosion, scaling, and biological growth. Use filtration systems to remove particles, and for water-cooled systems, add anti-scaling agents or biocides as needed. For glycol-based systems, monitor the concentration and replace degraded fluid to avoid damage.
Clean, properly treated fluid helps maintain efficient heat transfer and keeps the chiller running reliably.
5. Add a Variable Speed Drive (VSD)
Chiller motors are usually the largest single electrical load in a building. Most constant-speed compressors match capacity to load by using inlet vanes, which restrict the amount of gas that enters the compressor impellers.
However, this method isn’t very efficient at modulating chiller capacity. You can use variable speed drives to increase energy savings in the machine. They reduce the inrush current of the motor to nearly the same level as the amps used when operating at full capacity.
6. Increase Supply Temperatures
Most types of chillers are designed with a chilled water supply temperature to ensure proper dehumidification and an adequate supply of air temperature for occupant spaces during peak times. However, the system often fails to reach these peak weather conditions. Increased water supply temperature reduces the amount of energy required to transfer heat from the fluid to the refrigerant, resulting in higher water chiller efficiency.
Example: Raising the chilled water supply temperature by just 2°F can cut energy consumption by up to 3-5% in a commercial building without impacting performance during mild weather.
Get the Most Out of Your Chiller in 2025
Cold Shot Chillers is dedicated to ensuring that your business has access to the most efficient chillers for your operations. Upgrade to our dependable air-cooled and water-cooled chillers, designed to maintain ideal temperatures for your goods and machinery while maximizing energy efficiency.
Feel free to contact us today for more information about our high-efficiency chillers!