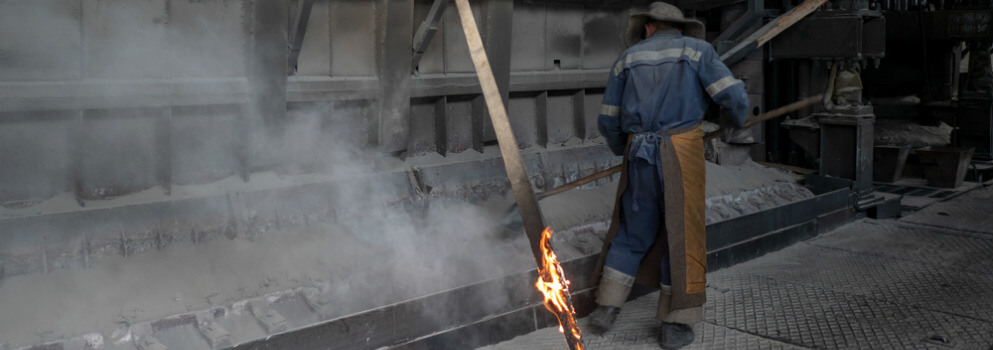
MAINTAINING ANODIZING TEMPERATURES WITH AN ANODIZING COOLING SYSTEM
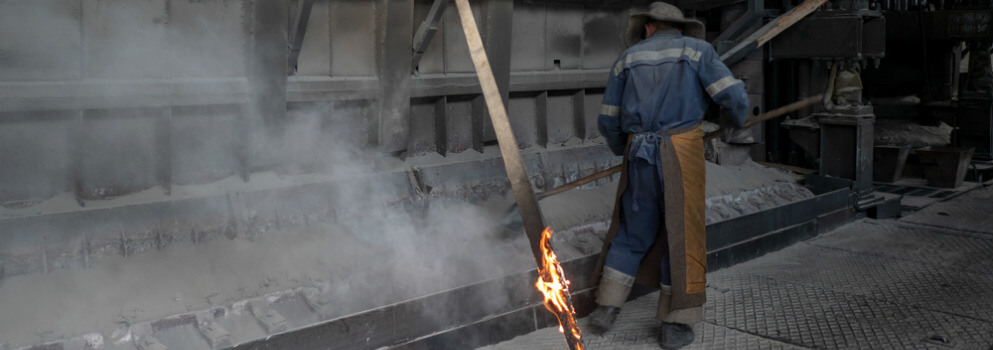
One of the major issues players in the metallurgical industry must contend with is metal corrosion. These industries utilize various techniques to improve the properties of their products. A popularly employed means of creating a corrosion-resistant and ornamental finish to metalwork is by anodizing. Having a properly functioning anodizing cooling system will go a long way in the performance of your metal finishing process.
What Is Anodizing?
Anodizing is a chemical process that adds a layer of natural oxide to the surface of metals. The term anodizing is derived from how the chemical coating is carried out. The metal piece to be anodized forms the anode terminal in an electrolytic cell.
Which Metals Can Be Anodized?
While aluminum constitutes the most commonly anodized metal, other materials such as magnesium and titanium can also benefit from anodizing processes. Although anodizing has its advantages, some materials should not be anodized. Carbon steel, for example, will undergo rapid corrosion after exposure to an anodizing reaction.
How Does Anodizing Work?
The metal to be coated undergoes a chemical process where it is submerged in a vessel containing an electrolytic solution. The metal is made the anode while another electrode is designated as the cathode. An electric current is then passed through the acidic solution which dislodges hydrogen from the cathode as oxygen simultaneously forms on the surface of the anode.
Overall, the electrochemical reaction will serve to deposit a metal oxide film on the anode. The thickness of this film is determined by the duration of exposure of the anode to the current.
Why Are Metals Anodized?
Metal anodizing is done for several reasons to ensure the anodized materials become more durable, long-lasting while expanding the range of applications they can be used in. Outlined below are the top reasons why metals undergo anodizing.
Improved Resistance to Corrosion
Materials that will be used in high humidity/ water exposed environments benefit from anodizing their metal components. For example, boat and ship hulls, oil rig superstructures and dockside equipment all require a corrosion-resistant coating which anodizing can satisfactorily provide.
Metal Hardening and Abrasion Control
The strength properties of metal can be improved significantly by subjecting it to anodization. Aluminum that has not been oxidized (in its non-anodized state) is soft and unsuitable for applications that require sturdy components. By comparison, aluminum oxide is valued for its high tensile strength and is used in the manufacture of wear-resistant aluminum alloys.
Dyeing and Metal Ornamentation
The oxidized layer created during anodizing is a porous one. Ornamental metalworkers use this to their benefit and introduce absorbable dyes to the oxidizing process to create a variety of brilliant metallic colors that can have a broad range of artistic and commercial uses.
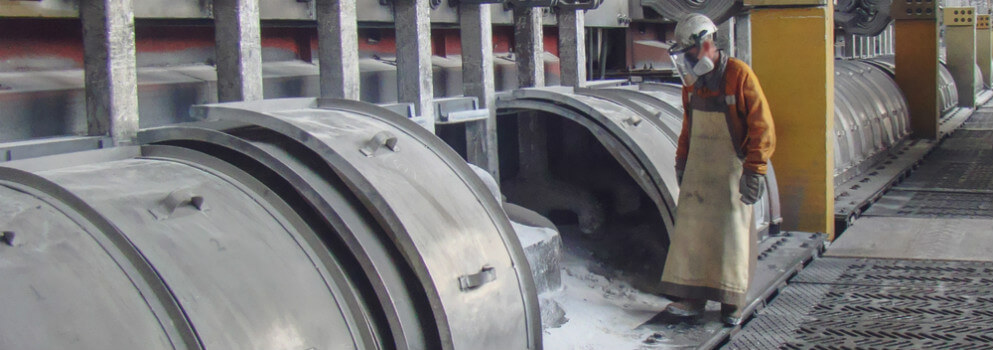
Developing the Right Anodizing Cooling System
As occurs in a majority of chemical and electrical processes, a significant amount of heat is generated during an anodizing session. Generated heat must be properly dissipated from the anodizing process to ensure even oxidization.
The most effective way of regulating anodizing temperature is by using an anodizing cooling system. Most oxidation plants use either a water-cooled chiller with a cooling tower or air-cooled chiller to achieve an optimal anodizing temperature.
How Does an Anodizing Cooling System Operate?
Both air-cooled and water-cooled chiller systems can be installed alongside the vessels containing the electrolytic fluid. The mechanism of cooling is straightforward. A fluid refrigerant is circulated through a metal finishing chiller, which then circulates through a heat exchanger to cool your anodization process solution. The warmed refrigerant is sent back to the chiller to repeat the loop.
Temperature changes within the anodizing vessel are detected by a thermal regulatory device installed inside it. When there is an increase in the amount of heat being generated by the anodizing process, regulatory valves in the chiller system are opened either automatically or manually to allow coolant flow through the heat exchanger and cool the vessel. These valves are shut off when optimal temperature ranges have been restored to avoid overcooling the electrolytic process.
An alternative method of regulating anodizing temperature is using cooling coils which are immersed directly into the anodizing solution. Although this method is less costly to install, it has some drawbacks when compared to a standard anodizing cooling system that operates with an external heat exchanger.
- Thermoregulation is less precisely controlled.
- Cooling coils may leak, introducing refrigerant into the anodizing vessel causing contamination and disrupting the oxidation process.
- There is a risk of electrolytic chemical corrosion of immersed cooling which will drive up operating costs.
Cold Shot Chillers Can Meet Your Metal Finishing Needs
For over three decades, Cold Shot Chillers has provided the best industrial water chillers for a wide range of processes. If you’re looking to invest in a top-quality metal finishing chiller, our experienced and dedicated staff will be happy to guide you through the selection process.
Please contact a member of the Cold Shot team today to learn more about how we can help with your process cooling needs.
