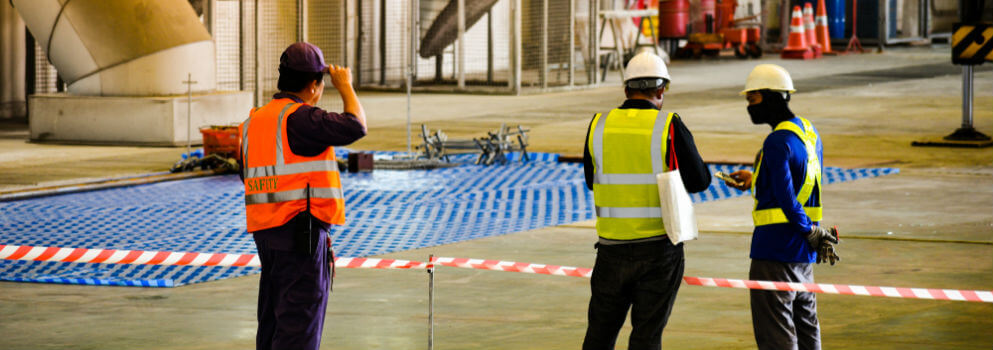
HAZARDOUS AREA CLASSIFICATION – WHAT IS EXPLOSION-PROOF CLASSIFICATION?
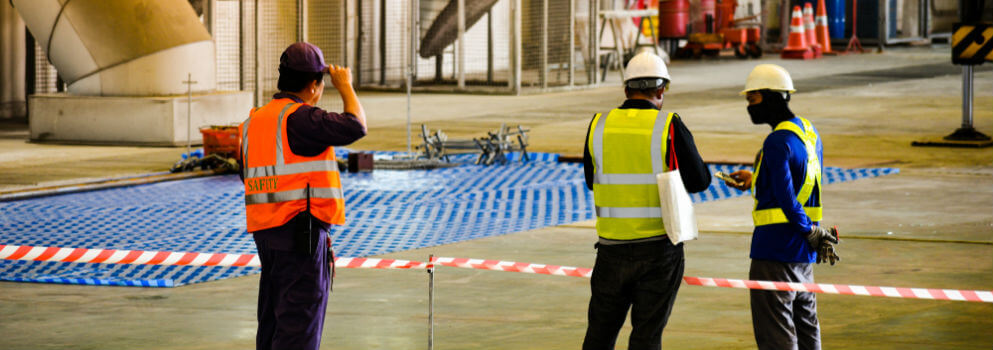
A major hazard associated with industrial production processes is the risk of explosion. Manufacturing processes may generate or require the use of potentially ignitable dust or vapors. If these combustible gases are not properly channeled, there is an increased risk of them being ignited leading to a serious injury to personnel and/or damage to machinery.
To understand how to prevent these explosive situations, the location and types of potential hazards should be identified and categorized. In this article, we will consider various hazardous environment classifications key to preventing industrial disasters.
What Is Hazardous Area Classification?
Hazardous classified locations are environments in which there is a potential risk of fire or explosion due to their containment of volatile gases or dust. Hazardous area classifications are a grouping system that recognizes the risk associated with various volatile materials and determines the appropriate protection measures needed to mitigate that risk.
Electrical Hazardous Area Classification
The standard electrical classification for hazardous areas implemented in the United States and Canada is the system proposed by the National Electric Code. This system of classifying electrical equipment in hazardous areas is based on a class/division system which defines the nature of hazard-prone material, and the probability of it being present in an industrial environment.
Class
The class component of an explosion zone classification system determines the properties of hazardous materials present in any given environment. Hazardous materials are categorized into three main groups:
- Class I environments where hazards are flammable vapors and gases present in sufficient quantities to form explosive mixtures
- Class II hazardous materials are combustible dust present in quantities enough to trigger an explosion or ignite a fire
- Class III materials are fibers or flying particles present in an environment. These materials may or may not be sufficient to cause an explosion or start a fire
Division
An explosive atmosphere classification also considers the probability of potentially hazardous material being present in an environment in concentrations enough to cause an ignition. Two main divisions are recognized below:
- Division 1 substances are classified as high probability materials. They have an increased chance of creating an explosive or combustible mixture as they are intermittently or continuously generated around machinery working under normal conditions
- Division 2 hazardous materials have a lower probability of creating an ignitable or explosive situation. These substances are only generated when equipment is operated under adverse conditions or when there is a system component failure
Group
The hazardous area classification guide for groups divides the type of potentially explosive material contained in an environment into the six groups listed below:
- Group A indicates environments containing acetylene.
- Group B atmosphere contains a potentially explosive gas, liquid or a mixture of an ignitable liquid-produced vapor and air. These volatile air, liquid, and gas mixes have a maximum experimental safety gap (MESG) value of 0.45mm or less, and a minimum igniting current (MIC) ratio 0.40 or less. Group B gases include butadiene, acrolein, and propylene oxide.
- Group C atmosphere contains a potentially explosive gas, liquid or a mixture of an ignitable liquid-produced vapor and air. These volatile air, liquid, and gas mixes have an MESG value greater than 0.75mm and a MIC ratio greater than 0.4 but less than 0.8. Examples of gases in this category include carbon monoxide, hydrogen sulfide, cyclopropane, and ether.
- Group D environments are composed of flammable gases, liquids or a mixture of a combustible liquid-produced vapor and air. These air, liquid, and gas mixes have an MESG value greater than 0.75mm and a MIC ratio greater than 0.8. Examples of hazardous group D gases are ammonia, methane, vinyl chloride, and naphtha.
- Group E includes hazardous metallic dust of aluminum, magnesium, bronze, zinc, chromic or titanium.
- Group F includes carbonaceous clouds of dust (carbon black, charcoal, coke and coal).
- Group G encompasses all forms of combustible dust not present in groups E or F. Examples are grains, starch, wood, plastics, and chemicals.
Intrinsically Safe Definition
Intrinsically safe equipment is defined as an apparatus with circuitry where sparks or other thermal effects, are incapable of igniting an explosive mixture of volatile materials or gases under predetermined test conditions.
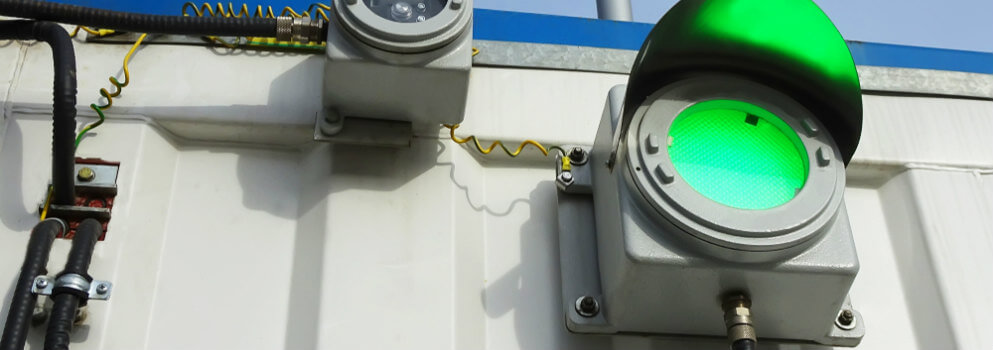
How to Comply with an Explosion-proof Area Classification?
Compliance with explosion-proof classifications depends almost entirely on the use of the right apparatus in workspaces. Explosion-proof equipment with components that can prevent the ignition of sparks within a potentially combustible space is highly recommended.
Cold Shot Chillers Has Explosion-proof Chillers
For over three decades, Cold Shot Chillers has served as a chiller manufacturer of highly durable and reliable units. Our prioritization of customer satisfaction and consultative approach to doing business will ensure that you get the best quality of service possible.
Please check out our custom explosion-proof chillers that can be suited to various industrial and commercial applications.
For more information about how we can help fulfill your process cooling needs, please contact us online today!
